What’s up, dock? Bugs-Bunny references aside, why are more eCommerce players preferring cross docking over traditional fulfillment as a logistics strategy?
In supply chain management, time isn’t the only thing of essence; it’s accuracy and costs too, and in an “I-want-it-right-away” economy, all sellers are expected to drive zero-error and no-lag fulfillment.
Dive right in with us as we go over cross docking, who it’s best suited for and benefits of implementing it as part of your warehouse management system.
What is Cross Docking?
Cross docking is a supply chain efficiency strategy that directly transfers products from inbound vehicles to vehicles intended for outbound shipments, bypassing traditional warehousing.
There’s no storage involved due to immediate unloading and loading which ultimately expedites last-mile logistics.
Goods are received at the docking terminal and are then passed to the shipping dock for immediate loading which saves time, storage cost and facilitates quick updation to inventory levels.
Companies use cross-docking to
- Consolidate several small shipments from several suppliers into one for bulk shipping which helps save shipping costs. These merged shipments are usually stowed in a staging area separately until enough is accumulated for a truck.
- De-consolidate products from a bulk shipment for delivery to retail stores which works for DTC fulfillment.
- Organize items for efficient delivery to retail outlets, customers or fulfillment centers.
Cross-docking reduces storage and fast-tracks fulfillment by bringing the inventory closer to the end consumer.
What happens inside Cross Docking?
In cross docking, where you are spending every minute counts to ensure accuracy in execution and completion.
- Inbound : the products reach warehouses by land from various suppliers and destinations.
- Dock scheduling: Warehouse operators roster vehicles in slots to avoid congestion at the terminals.
- Loading docks: There are multiple and separate docking stations for loading and unloading that facilitates smooth goods handovers and avoids mixups.
- Labor force: A specialized task force will be required to conduct quality inspections before sortation and loading in a short span of time.

Benefits of Implementing Cross Docking
Does your enterprise deal in products that are expiry-sensitive or in high-demand?
If you answer yes to the above question, you will benefit from cross-docking because the single biggest advantage it offers you is that it wastes no time in getting demanded items quickest to your customers, whether they are actual shoppers or distribution hubs. Here are some more benefits to cross docking
Early or Timely Deliveries
Cross docking eliminates hold ups and confusion by readying items for fulfillment at designated docks or terminals. Even the effort investment is brought down because you already have a dedicated team for it which frees the rest of the warehouse operators’ time from the busywork of searching, traveling, picking and packing.
Easier inventory management
The receiving inventory is easier to account for as ground movements are live, which allows for quick channel updation. Sellers need not worry about excesses and shortages. Cross docking eliminates the need to scan the inventory and store details into a WMS because levels are updated based upon actual activity.
Saves on storage costs
When inventory moves in minutes, you don’t need to rent out an entire warehouse section long-term, which reduces overheads such as utility. It optimizes space by clubbing the sorting, distribution and shipment assignment in one central hub, which saves time, labor and fulfill in bulk, making it a great option for B2B fulfillment.
High inventory turnover
Cross-docking operations simplify movement tracking and SKU management equipping sellers to maintain a high inventory turnover. More importantly, sellers can maintain accurate invent
Less chances for damage
When items are moved around a lot, there’s higher chances for it to incur damages from the handling and transportation, which cross docking eliminates. It also ensures perishables don’t sit at a warehouse until it exceeds its expiration date, retaining quality.
Reduced transportation costs
By utilizing the total trucking capacity on order volume, number of suppliers and peak demand, cross docking reduces the number of shipments to send out and takes full advantage of the mileage. With route optimization, more shipments cover larger geographical ground and expedite fulfillment for same day and next-day deliveries.
Cross Docking Vs Transshipments
Cross Docking and transshipments aka transloading are used at different points in the supply chain, but there are a few differences to tell them apart, which are outlined in the table below;
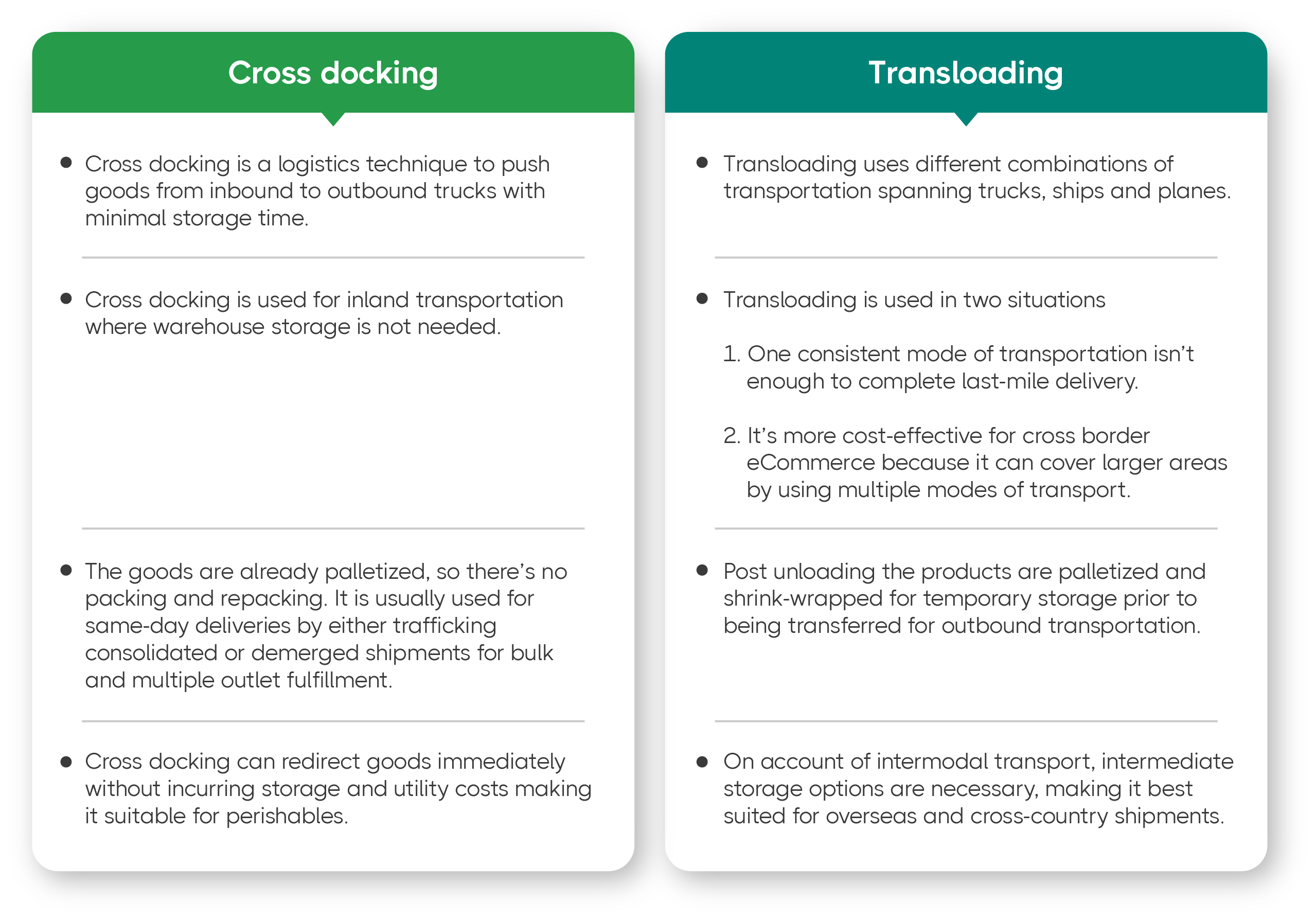
Cross Docking Gains by Industry
While cross docking is not a one-size-fits-all strategy, it can be immensely beneficial to industries seeing high order volumes with shorter turnaround times.
Below are some industry examples;
- Retail
Fresh produce for daily consumption such as fruits, vegetables, dairy and meat need to be transported quickly from supplier to customers to avoid spoilage, which is why grocery chains and supermarts use cross docking to restock shelves. With item-ready racks waiting, customers will always pick up fresh inventory right off the shelf.
- Healthcare
In emergency situations that make the literal difference between life and death, cross docking proves invaluable in streamlining medical distribution. In reducing the handling steps, it speeds up procuring essential hospital supplies and lifesaving drugs.
For example, a leading Indian biotechnology stem cell bank uses warehouse EDD routing logic to prioritize sample collection and route expiry-sensitive samples to a particular location. This has helped the company to manage an inventory of 40K+, reserving portions of it by FEFO logic [i.e. by expiration date] to ensure zero-waste.

Cross Docking Types
Depending on need, there are several use cases for cross docking which are
- Manufacturing: Items for production are delivered to the manufacturing site by clubbing them. Another example of manufacturing is collecting goods from different vendors for direct deliveries to customers. Think of the supply of auto spare parts to showrooms.
- Distributor: In this type of cross docking, products are consolidated from a centralized distributor hub accommodating various suppliers for fulfillment to individual retail outlets. For example, the Landmark Group carries different brand labels under the clothing segment.
- Retail: Retail cross docking sources materials from different vendors and delivers the grouped items in bulk to retailers. This is further split into seasonal inventory and FMCG inventory, where the latter’s stock replenishment is more predictable than the former.
- Transportation: Shipments are consolidated from different suppliers with a common destination zone in mind, which optimizes transportation times and cost. It applies to less-than-truckload shipments where the loading trucks aren’t at capacity but are still able to fulfill small deliveries.
- Pre-distribution cross-docking: Products are unloaded, sorted and repalletized according to distribution instructions. In this type of cross docking, the inventory doesn’t sit put for long and is suitable for retailers doing their own fulfillment.
- Post distribution cross docking: Is the opposite of pre-distribution, where the goods are stored in a temporary facility awaiting further instructions for the next leg of the journey . This is suitable for retailers who wish to use the time to strategize which locations to ship inventory to or which warehouse to forward excesses to based on existing levels and cycle counts.
How to Introduce Cross-Docking in Your Supply Chain
If you choose to use cross docking in your supply chain, it needs an automated shipping management solution that aggregates courier partners and lets you set triggers and thresholds to prioritize expiry and time-sensitive item movements. The steps to follow to integrate cross dock systems are as follows
Assess current logistics requirements
Cross docking requires you to expand your infrastructure and labor budget to accommodate docking terminals or stations, loaders and quality-inspectors. You may need to use a mix of intermodal transportation, which would also mean temporary storage and staging spaces, in which case transshipping may work out to be more cost-effective than cross docking.
Evaluate supplier reliability
Cross docking operations fall apart at the seams if your suppliers are habitually tardy. So, based on supplier-relationships, prioritize those who are dependable to ensure shipments reach you on time. Regularize communication for seamless ground-level coordination.
Create docking schedule
Eliminate double bookings and conflicts with a detailed schedule that indicates who are on duty for dock management, quality inspection and outbound preparations. Remember to add a buffer for unexpected disruptions.
Invest in automated SMS
A shipping management solution can give you inventory tracking and plug in supplier and shipment scheduling information, arrivals and estimated delivery dates, updating quantities and fulfillment rates accordingly. Even better if the shipping management system integrated with a warehouse management solution because you can then reduce the communication ping-pong between parties. The collective efforts of mobilizing autonomous and vehicular fleet, real-time barcode scanning and routing optimization helps shorten distances and reduce travel and updation time.
Conduct and review efficiency improvement exercise
Identify opportunities for improvement by reviewing shipping SLA and key metrics to adjust based on data-driven insights. Examples of features that can be configured through the EasyEcom system includes auto batch creation, paperless picking via HandHeld Terminals or devices (to drive QC-scans) and loading time by shipper or courier partner. The ultimate indicator of efficiency improvement is the reduction in manual intervention and time!

Taking the Dock-tor’s Advice
eCommerce has increased the pressure on logistics companies to get orders to customers accurately, efficiently and promptly. All this is to be balanced against costs. Cross docking isn’t the right choice for every industry, but those that do not need warehouse storage and wish to bridge the distance and transit time for their end-customers should definitely consider streamlining last-mile logistics with cross docking systems.
FAQS
What are cross dock warehouses?
A cross-dock warehouse is designed for quick goods transfer that are fit for shipping. Goods arriving at this facility are quickly unpalletized and repacked into trucks at their maximum capacity.
How are cross docking and warehousing different?
The difference between the two lies in the amount of storage time that products spend in the facility. With cross-docking, this time is very little while warehousing can store products for months according to demand fluctuations.
What cross docking warehouse design best practices should be followed?
The ideal warehouse layout for the cross docking approach are I, T and X- shaped configurations. This will prevent vehicular congestion and reduce the distance between inbound and outbound trucks for accessible unload and reload points.
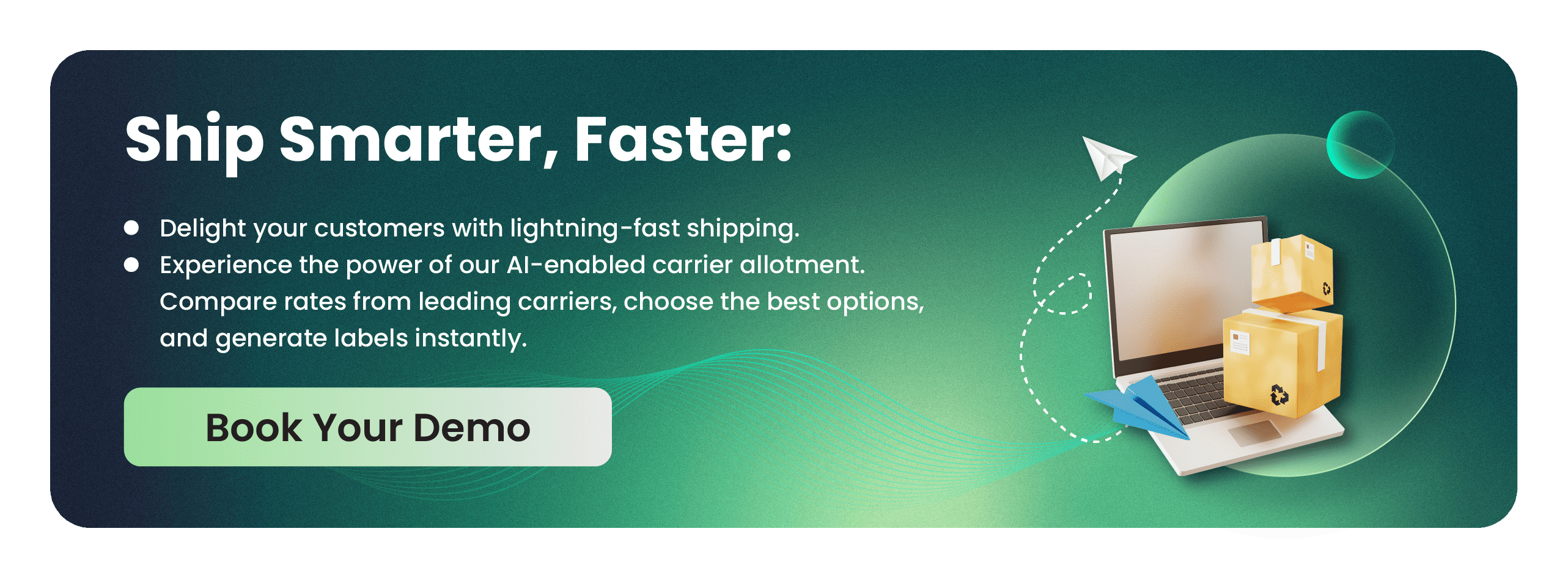