To begin with, from suppliers and manufacturers to retailers or customers, implementing a warehouse management system (WMS) allows an organization to optimize all the warehousing activities, minimizing labor expenses, and improves inventory accuracy.
And, one wrong step towards warehouse management can lead to workplace accidents & major loss of efficiency. We will discuss that later in this article.
Let us first understand why automating Warehouse Management is important and when should one be planning to go for WMS.
Why and When should you plan on implementing a warehouse management system (WMS)?
WMS systems are meant to automate and implement tracking for day to day activities of a warehouse. Locating a particular item within the warehouse can be challenging for a large warehouse with multiple staff members. WMS takes out that pain. Its applications go beyond just that. WMS is capable of monitoring product quantities, cycle counting, picking, packing, shipping, and managing multiple locations.
Following are the indicators to implement WMS:
- You have multiple warehouses
- You fail to dispatch orders within specified SLA
- It’s difficult to track your shipments and returns
- You find it extremely time-consuming to search for a product in the warehouse
- You process more 30-40 orders a day
- There is more than one employee doing the picking and packing job
WMS implementations are usually time-consuming and require substantial efforts. Please be assured to have a dedicated internal team to manage the transition process.
So what if you are not ready for such commitments? What system to operate on if not WMS? You can opt for another similar category of software called Inventory Management Solution (lMS). Let us first understand the difference between WMS and IMS.
Difference between inventory management system and warehouse management system (WMS):
Inventory Management is one part of warehouse operations. To manage inventory on a large scale, WMS platforms are deployed. WMS is usually, more complex to set up as compared to managing inventory through IMS (Inventory Management System).
IMS involves tracking the count of an individual product whereas, WMS involves tracking the product space along with the shelf and bins. It helps you manage warehouse space more effectively.
Unlike an IMS, what makes WMS a larger part is, its connectivity to the overall management systems involving, products supply, sales, distribution, and quality management.
Both inventory and warehouse management systems enable companies to use bar-coding devices to track, bill and update the inventory. It also provides with picking, packing, and shipping information for delivery, managing multiple locations, and perform cycle counts.
Benefits of Warehouse Management System
The WMS system integrates the workers, task handling types of equipment, storage tracker onto a single programmed software called as WMS. It helps avoid manual errors by working on system directed operations of receiving, putaway, picking, and shipping. Some of the major benefits are below:
- 100% Inventory tracking
Systematic tracking of inward, outward and movement of stock within the warehouse will ensure complete accuracy and avoid any shrinkage. Item level barcoding enables the complete history of a particular item in case a product is RTO and gets re-shipped etc
- Detailed Quality Control at Receiving
The system facilitates detailed QC process at the time of receiving to ensure only the correct product gets inwarded into saleable inventory. Rest gets tracked as rejected and can be later returned to vendor etc. This ensures a high level of customer service and major costs savings in case of miss-shipments by the vendors.
- Save space and maximize space utilization in the warehouse
With handling your inventory in the right way, you will be able to effectively minimize overstocking and under-stocking of products. In other words, it enables accurate stocking, slotting and pulling orders.
The system guides an operator on where to put an item, maximizing utilization of each slot by selecting a storage path that best fits the product.
- Increased productivity in the warehouse
The employees get to know the exact location of the product's shelf. This reduces the time and risk of stretching the period. The staff gets to pick more orders in less time, increasing efficiency in the order fulfillment process.
- Accurate Inventory planning
Get insight into most popular products during a specific time period. This will help you decide which products to invest in at that time.
- Keep a check on received products
Keep a record of received products and ordered products handy with GRN report in order to avoid paying extra to the supplier. It ensures all the delivered items are correctly recorded.
- Increases customer satisfaction
Ensures prompt and accurate product delivery. This helps in reduction of customer complaints and an increase in on time delivery.
- Improved Security
Unfortunately, there are employees who try to steal or unintentionally damage the products. A WMS system helps you keep accurate records of inventory, providing you with user-specified logins so that, managers can ensure the staffs are not slipping extra products on delivery.
- Strong reporting
WMS captures various data points in terms of timestamp and user credentials. This data comes in handy when running critical reports like Inventory aging, restock calculations, SLA deviations in fulfillment, etc.
- Perishable products friendly model
The WMS system also supports FIFO, giving flexibility to the managers of running their warehouse. FIFO model ensures expiring and perishable items are picked first.
Let us now see how a non-WMS enabled system can differ from a WMS enabled warehouse,
Non-WMS enabled warehouse Vs WMS enabled warehouse
If you implement a warehouse management system in your warehouse, you will come across a lot of changes in your daily activities and the profit margins.
What issues can a WMS system resolve?
Issue 1. While the inbound process takes place, a lot of unfinished tasks remain until the end of the day. This results in a double shift for the employees. With no proper serial no. and shelf assigned, it gets difficult to locate a product in the warehouse.
Solution: With a WMS enabled system, you receive, Proper documentation from the supplier along with the estimated time of delivery.
- The incoming products will then be auto-recorded with their bar-coding, serial no. and shelf through which it will make it easier to identify a product and its location.
- With this, labor productivity will increase and it will not take much of their time to locate any product in the warehouse.
Issue 2. Normally a non-wms system doesn’t prioritize the shipments because of which few customers might have to deal with late deliveries and this will result in a dissatisfied customer.
Solution: A WMS enabled system will priorities your orders accordingly and will prompt you on the deliveries exceeding the delivery time.
Issue 3. You might sometimes receive an update or sometimes even not receive an update on missing goods or incorrect count, and damaged products.
Solution: This issue can be resolved by monitoring the performance of employees, by introducing the RFID or barcode readers and allotting an individual for the task who cannot process any movements without any confirmation from the managers.
The benefits can go on. Comment below with your issues with managing your warehouse and we will surely get back to you with our possible solution.
Conclusion:
Choosing the right warehouse management system can add up efficiency and accuracy to the process by improving and maximizing the speed of every stage of fulfillment. It can help you improve sales and increase profitability with on-time deliveries, resulting in happy customers.
Are you looking for an omnichannel inventory management solution with integrated B2B order management for your eCommerce business? Drop us a line at care@easyecom.io or directly sign up for a demo here.
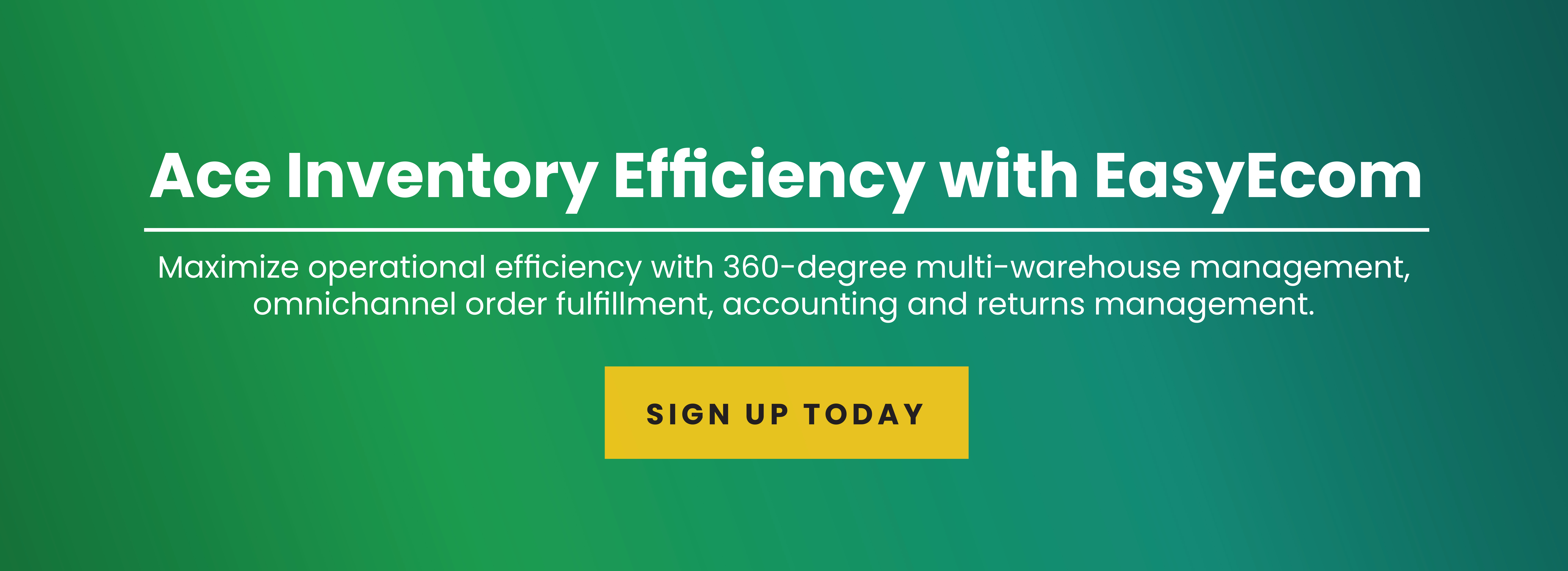