What drives lightning-quick, efficient and accurate fulfillment? Ask 10 eCommerce businesses this question, and you’ll get 20 different opinions in response. But the one document that everyone will concur is essential to streamlining order fulfillment processes with reduced costs and efforts is a picklist.
With several concurrent tasks, a warehouse is always guaranteed to be busy, but it shouldn’t turn into a maze, especially when time is of the essence. Every eCommerce enterprise needs to prioritize where most of it goes to maximize productivity and ensure that interdependent tasks aren’t delayed or blocked. On a massive scale, one of the biggest inefficiencies is in order picking, where 50% of the time goes into walking in search of the correct items for an order. When you realize you’re paying your laborers for their footwork rather than the actual picking, that’s when it hits you how processes fall apart without a picklist.
Know what a picklist is, but not how useful it is in bringing down congestion and speeding up fulfillment? Dive into this picklisting guide!
What is a Picklist?
Imagine speeding through your warehouse with a clear, concise list that ensures you never miss an item or pick up the wrong item. That is how a picklist helps you stay well-organized! A Picklist, a.k.a picking list or pick ticket, is a document used in many industries that specifies the quantity of items from a particular storage area for order fulfillment and task completion.
It makes the picking process organized, shorter, accurate and efficient so that picking operators find what they’re looking for and know what equipment or tools are required to handle the items with care.
Think of how you would shop at a grocery store with a list in hand. Rather than ping ponging between aisles, you would bucket the items you need into categories, such as food, cleaning equipment etc, head to that particular aisle and spend some time in it to get everything belonging to that section before checking out. A picklist works in a similar fashion, helping to organize your warehouse.
Usually, picklists are generated through a warehouse management system which makes the fulfillment operations paperless. Physical processes aren’t completely phased out though, because small inventory requires lesser efforts, so warehouse teams can manually administer paper picklists that suit any environment and are easier and cost-effective. However they’re imprecise and invite a mounting paper trail that compounds inventory management down the line.
Digital picklists, on the other hand, are portable and accommodate more information without constraining workers or eating up more time. In fact, workers can be seen wearing or carrying a device that receives order data in order to generate the picklist electronically.
Picklisting can seem a trivial thing to pay attention to for enterprises with smaller inventory and a handful of SKUs that are easy to locate and track sans a picklist. But as your order volume grows and more hands are onboard, you’re going to need something that optimizes effort hours and reduces search times, considering that pick-and-pack services cost 36.4% more for B2B than B2C items, according to CapitalOne Research.

A picklisting system within automated WMS helps organizations determine the most efficient picking method to fulfill customer orders. bor accounts for the biggest portion of the cost of warehouse operations.
On the EasyEcom WMS and Android based systems, you can create picklists in two modes, namely
- Normal Process
The Normal process(also known as piece picking) is straightforward, and requires the user to navigate to new orders under “Orders” and download the picklist sheet using the “Print Picklist'' button. The normal process is where every order has its own picklist and applies for order picking one at a time. This processes orders independently and can maintain order accuracy for tailored requirements.
- Batch Process
Batch processing is a setting that needs to be activated from Account settings in order to process large order volumes in a shorter time frame. Batched picklists usually contain multiple items of a similar nature that are grouped together to get around to more orders. It saves travel time and closes the distance within the warehouse because one trip satisfies several orders. Upon picking the batch, it is then sorted and separated for order fulfillment.
The choice of going with normal or batch picking comes down to order volume, facility layout, warehouse design and workforce size. Interestingly, multiple warehouses with fewer staff will stand to benefit the most from batch processing given the shortage of hands and amount of work!
What should a Pick List Contain?
The information you see on the pick list is normally slotted into top, middle and bottom sections. This visually helps the picker to determine composition and identify the item through details such as its SKU, quantities, the warehouse it is sitting in and an image to help match its description. The top section includes
- Order number
- Manufacturing and/or Expiry Dates (if perishable)
- Warehouse location
- Shipment type & number
- Handling Fragility or sensitivity
Depending on how much detail will benefit the picking team, the middle section of a picklist can list its aisle number, storage type, units required and even how many SKUs are left, which confirms inventory levels and ensures accuracy every time picking is initiated and completed.
The bottom section of a picklist can optionally have a space for comments or feedback along with signature boxes for the required authorities to sign off on, such as the picker and dispatcher.
Picklisting In Action: Category-Specific Use cases
How does a picklist management system contribute to reducing turnaround times (TAT) and in ensuring eCommerce and B2B enterprises adhere to SLA? After all, your Warehouse shouldn’t be a Where-house that confuses your pickers and extends the pick-pack-ship process! Let’s examine a few use cases by industry ;
Beauty, Personal Care and Cosmetics
A leading commerce company in the beauty and cosmetics segment was used to manual picking processes and wanted a solution that could replace it in order to save time and process more orders. Through EasyEcom’s HHT and auto batching feature, they seamlessly transitioned from physical-to-digital picklisting, going paperless and automating task creations.
Some of the system benefits this beauty unicorn experienced in mere weeks include
- Going 100% paperless to spend less time in picklist identification and assigning pickers to expedite activity.
- Picker reassignment to reshuffle operators and avoid lane and aisle congestions.
- Priority picklisting for brands with multi-channel listings
- Reduced time in identifying the first marketplace order to be processed in the order of preference,i..e Flipkart>Amazon>Nykaa>Native website.
- Enhanced visual picklist management with image-based identification.
- Instant identification of recently imported orders for batches created right after generation.
- Saving time in creating batches with timely communication on batch priority and description.
- Monthly and Daily Reporting analytics on pick-pack processes that compare current assignments with picking efficiency, helping to determine future reassignments and allowing the business to track picker efficiency on an individual-level.
- Drove positive customer experiences with an accuracy rate of 97.99% with order identification automation, preventing incorrect item grouping that would have otherwise created a Chinese whisper in item dispatch and shipping.
- Bifurcate orders with tags to distinguish the difference between personalized/custom and regular orders to ensure the pick-pack-ship process experiences a smooth, undisrupted flow.
- 100% activity-improvement with unit-wise, batch-wise and packing efficiency.
Home Decor and Furnishing
A leading eCommerce brand specializing in heavy duty home essentials succeeded in
- Driving sortation accuracy with ~100% by redesigning their warehouse layout to accommodate zone picking, aisle and racks.
- Utilizing the auto batching feature to process 10 batches containing up to 100 orders within minimal time, frequency and units.
- Doubling picking efficiency from 45% to ~90% with android-based task automation, ensuring absolute operator safety at all times.
Food and Beverages
A global confection conglomerate experienced fulfillment errors from disrupted order flows, which blocked offline replenishment . Within a year of using the auto batch picklisting feature within the EasyEcom system, the titan chocolatier was able to
- Automate picklisting and redefine SOPs by separating batches through handling requirements, order sources and SKUs.
- Expedite order processing by 4x with batch and custom order identification. The enterprise was able to correctly identify composition in a shorter time span, thereby speeding up the processing for both standard and personalized orders.
- Identify batches to be processed first on priority according to the Statement of Purpose (SOP) to ensure zero-error and no-lag fulfillment.
- Reduce the communication trail by 30% with uncompromised clarity, saving 40% of processing time for several batches containing up to 50 orders per batch.
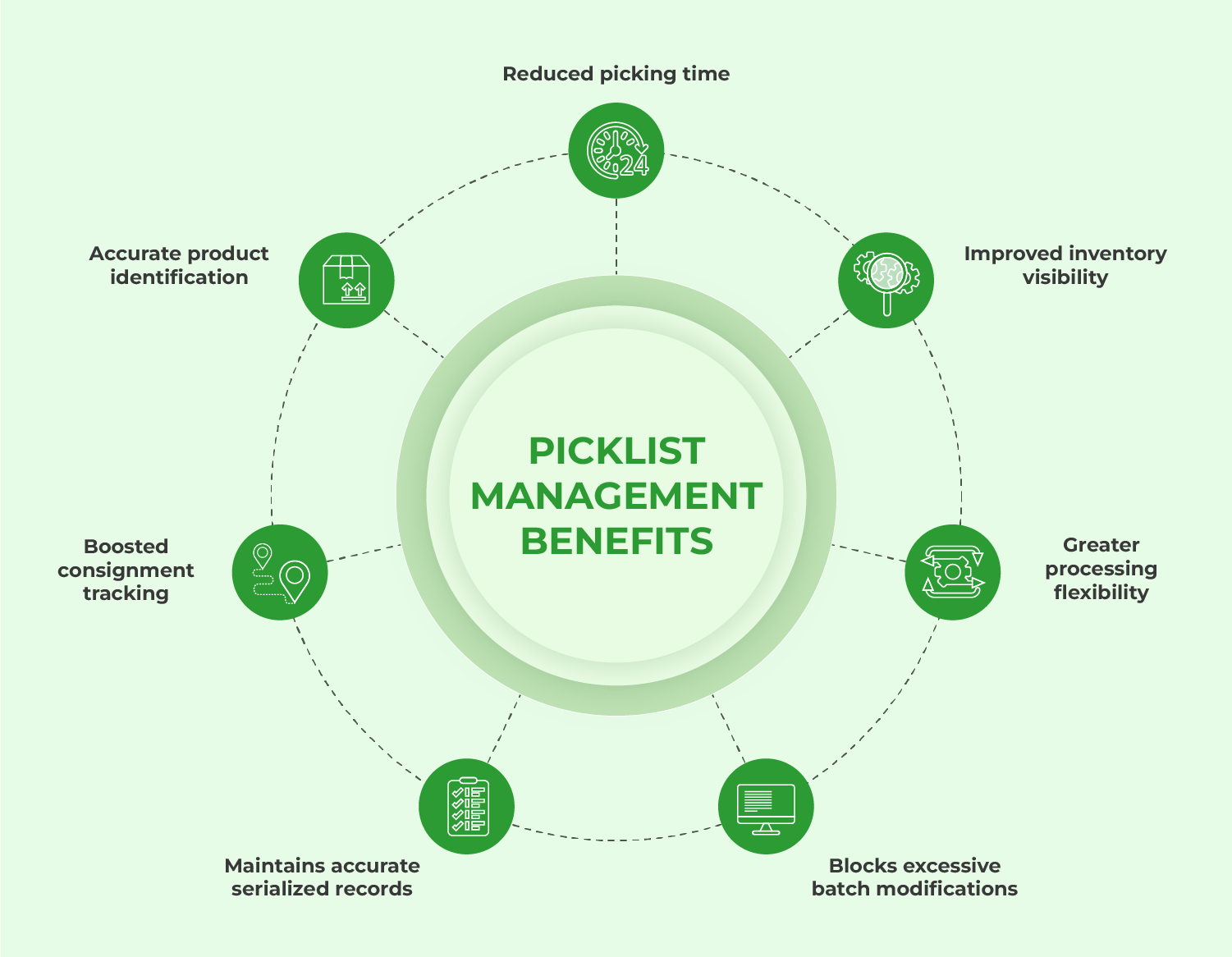
Benefits of Picklist Management
Improved inventory visibility
A WMS system helps pickers gain absolute visibility by recording expiry dates for perishable produce belonging to B2C and wholesale orders. And manufacturing dates for all b2c orders.
Reduced picking time
Constant movements require users to be mobile and use apps and tools. Through EasyEcom’s WMS android app, accounts that have wave picking and pigeon hole enabled lets pickers view details of the next station that they should make their way to through the picklist page.
Put simply, the picklist guides pickers to the right item and location, ensuring there’s no congestion. Organizations that use zone and batch-picking stand to benefit from this because it assigns pickers to zones and informs them of where to go. For example, if an order contains single items, the system will direct users to the packing station and similarly to the sorting station if multiple items are involved.
Accurate product identification
If you specialize in printable clothing and accessories, the Print On Demand function has enhanced picklists that are generated to record details such as color, size, SKU which ensures the warehouse team picks the correct product. For example, a blue shirt of a certain SKU code can sport different customizations and be mapped to the right order and customer (for example, one blue shirt can have Batman while another in a different color can have Bart Simpson caricature).
Inside the EasyEcom panel, the order picklist contains international EAN codes and MRPs to identify and track wholesale orders during the pick-pack-ship process to guarantee accurate shipments.
Blocks excessive batch modifications
Frequent updates to a batch can create discrepancies in inventory and picklist details. Through a WMS system, users can restrict new entries for batches already under process to ensure inventory levels reflect recency and new availability.
Maintains accurate serialized records
Depending on the customer, date of order received and shipping urgency, there may come a time when those eCommerce sectors that serialized their inventory may need to swap items. Picklists help to maintain a uniform and accurate record even if teams swap inventory items at the packing station for the same batch. For example, if a batch picklist mentions serial XYZ1, but the warehouse team scans and packs serial XYZ 2 instead, the system will record XYZ2 as shipped and XYZ1 as the currently available inventory.
Greater processing flexibility
At warehouses, different tools such as Pigeon hole, totes (small plastic boxes that can be picked up and moved along a conveyor belt system) and handheld terminals are used which determines the processing of B2C or B2B orders. The EasyEcom system offers users a configurable Bins Master through which these tools can be selected. In the case of B2B, the WMS system will ask the user to scan the picklist ID before directing them to the packaging and sorting stations. B2C users are directed to a page that indicates respective scanning functionalities. The flexibility reduces redundant scans and boosts overall processing efficiency and speed.
Boosted consignment tracking
Picklisting enhances B2B order processing by establishing stages through which the item moves. Through the EasyEcom system, for example, users can approve or disapprove quantities, select the zone and batch before assigning inventory and generate the picklist. The item is then sent for packing based on information available on the picklist from previous stages. The final step is that the consignment details such as invoice can be downloaded to have a uniform track on every moment until the customer receives their order.
In short, a picklist’s primary purpose is make a picker’s life easier by furnishing all requisite instructions and data that helps customers get their orders with zero delays, defects or damages. Every person in the pick-pack-ship process plays their role in synchrony, helping to orchestrate seamless selling!
Best Practices to Set the Picklisting Gold Standard
Picklist management helps your operations to run like a well-oiled machine. Some best practices to set the gold standard in picklisting are
Integrate WMS with Picklists
A warehouse management system (WMS) integrates picklists with inventory management systems and order fulfillment, which give system users end-to-end visibility from the moment sellers confirm the order to customers getting it safely.
The right WMS system updates inventory levels by offering visibility for adjustments and optimization at a bin-level. Warehouse operators can check and confirm levels and availability against inwarded quantities, recent stock counts, QC-checked returns to generate the correct, updated picklist. As the decision maker, you’ll instinctively know the system is right when you see it, but even so, let’s clue you in on some important factors in choosing a warehouse management software ;
- Affordability
- Scalability
- User-friendliness
- Integrability without data loss.
- Data integrity through role-based access.
- After-sales service and support.
Take these factors into consideration when choosing a WMS, and subsequently, picklist systems.
Regularize reviewing and monitoring picklists
While there’s no perfect picklist, it helps to regularly review the format and details of picklists and make changes wherever necessary to ensure relevant information is included. eCommerce businesses can then identify the potential for improvement and feature the fixes in the next iteration of order processing.
Train Warehouse Teams
Training is always critical especially if your business is doing a physical-to-digital transition for picklisting. New tools are involved, which will need considerable operating knowledge to ensure the person on the other side is reading the data correctly. Holding periodic training can boost productivity and safety and allow teams to get their burning questions answered .
At EasyEcom, we offer complimentary exploratory sessions as and when new features or upgrades to existing functions are rolled out, ensuring sellers are able to keep up with recent developments and experience undisrupted growth. We would recommend making use of these and empowering your warehouse teams with precise instructions, usage feedback and honest appreciation as part of the training quality.
Evaluate Current Picking Performance
Evaluate the current picking performance for speed, accuracy, adaptability and productivity in order to determine which areas could benefit from efficiency improvements, error reduction and augmented productivity. You can also choose to scale up or ramp down on features according to which ones are used the most and the least, helping to unblock bottlenecks.

Pick the Right Picking Methods
How can you determine whether batch picking, zone picking or wave picking works best for you when they each bring advantages to the table? Here is a brief revision of these terms to help you decide the best method for order fulfillment:
Batch Picking
- Processes multiple orders of the same item at the same time.
- Effective for subscription-based businesses where several customers order the same product.
- Reduces worker movements and picking time.
Zone picking
- Sections warehouses into zones, and each picker is assigned to a zone.
- Fulfills one picklist in unison by pickers passing the item from one zone to the next.
- Cost-effective
- Avoids overcrowding
Wave Picking
- A mix of batch and zone picking, where operators collect items from one batch and one zone.
- Picklist displays all items to be picked from current zone
- Batches move in waves across the warehouse until the packing station.
- Useful in large warehouses
As your eCommerce business grows, WMS is no longer an option you want to keep open. Ready to optimize your warehouse with effective picklists? Schedule a free demo with EasyEcom today and see the difference!
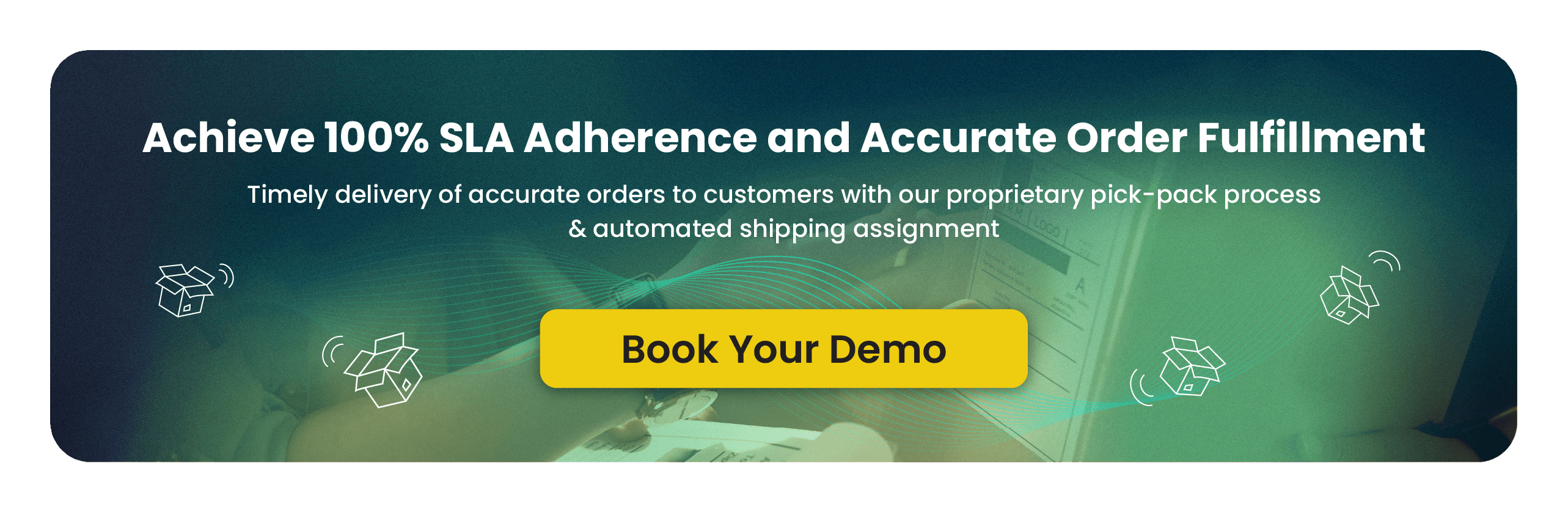