If you think about it, logistics demand an insane level of coordination and communication, particularly for those sellers who list their inventory across multiple sales channels and eCommerce marketplaces.
The picking and packing process is the bread and butter to your warehousing operations and determines order fulfillment success rates. It is the step that lets sellers reconfirm that they’re sending out the right orders to the right customers.
Let’s take you through order picking and packing processes in detail.
What is Order Picking and Packing?
Order pick and pack process involves locating and collecting the ordered items from inventory and sending them to the packaging station. In a fulfillment or distribution center, pickers collect the inventory items and send it to the packaging team who readies them for the courier partner.
Order picking is the first step in the chain that determines the remaining steps of packing, shipping and post-delivery. An efficient order picking process ensures that the right product is collected. Considering that all the items in an order won’t be located in the same part of the warehouse, picking involves travelling around the warehouse, which according to G2, accounts for nearly 50% of the total time consumed by warehouse workers.
Although it may seem like a basic process, order picking can be costly if the picking methods aren’t in line with warehouse size and eCommerce growth. Picking methods vary by order volume, and some are
Piece picking
In piece picking, warehouse staff move around and pick order items from shelves. They cross-verify the order description and SKU code before taking it to the packaging station.
Who is it right for: piece picking is the easiest method for small businesses that process a few orders a day.
Batch picking
In batch picking, you can categorize your orders into different batches based on sales channels, products ordered, payment type, customer location etc. These orders can be processed in one batch in a single go to eventually improve and increase your order fulfillment rates..
Who is it right for: Batch picking works well if your order volume is large enough to organize the items into batches. This way, one SKU code suffices for several orders carrying the same item. One The goal of batch picking methods is to reduce the back and forth around the warehouse.
Zone picking
If you’re considering the zone picking option, you should designate workers to specific zones in the warehouse from where they’ll pick products for each order. They have to pass this order to the worker in the next zone. Once the order moves through all the zones and is confirmed to contain all the items the order was placed for, it gets sent to the packing station.
Who is it right for: Zone picking is a reliable method for larger fulfillment centers and warehouses. You will need a warehouse management system to manage zone picking.
Wave picking
Wave picking constitutes a mix of batch and zone picking. Warehouse workers pick items within a zone for a batch rather than for a single order. This batch is passed to the next zone for picking.
Who is it right for: Wave picking is the best pick (literally) for fulfillment centers and large warehouses that process very high order volumes.
In warehousing and order fulfillment, the packing station is a physical workstation where workers determine the packaging material suited for the order in question by its product dimensions and weight. It will contain boxes, labels, packing paper, tape measures,glue guns and utility knives or scissors to enable the teams to wrap the item in a manner that minimizes chances of accidental damage.
How EasyEcom’s Packing Station Operates
EasyEcom offers eCommerce sellers the packing station and packaging material setting. When activated, the former will improve your packing accuracy while the latter ensures a damage-free shipment that best fits your order requirement.
The packing station feature optimizes the packing process by notifying you of the correctness of the inventory items being scanned. This ensures that the right orders are shipped out to the customers. Once all individual items have been scanned, the EasyEcom system automatically generates the invoice and label for an order, thereby eliminating the chances of wrong or incomplete orders.
The benefits of packaging via an automated pick and pack software are that
- The right order packaging material can be selected for the shipment, protecting its contents from extensive external damage.
- The system can track the product’s dimensions and weight to ascertain if the shipping cost deductions being levied by the carrier partner is correct.
Both the packing station and packaging settings can be activated from account settings.
In EasyEcom, the process of batching orders begins at the orders tab located on the left hand side.
- Under order batches, you can either add orders to an existing batch or create a new batch.
- Once you add the orders, assign the batch to a picker and print the picklist. You’ll see how many batches are ready to affix printed labels to, and how many are unconfirmed.
- The picker can locate inventory items and their quantities to bring them to the packing station table.
- Order processing can now start. The start processing button will redirect you to the process order screen. Click confirm to choose those orders you want to process in a batch.
- Select the packing station, inventory items and their SKU code, quantity required, quantity scan for all your confirmed orders. The quantity scan count will be automatically updated whenever you scan the SKU. The system has checkpoints in the form of sound alerts and pop up messages to help you make sure that you’re packing and shipping the correct inventory items to the customers. If you scan an SKU item that the customer did not ask for, it will alert you, thereby preventing an incorrect shipment.

Which is the Best Pick and Pack Method for Your eCommerce Business?
With most eCommerce businesses hitting the ground running with a modest order volume, it makes sense to run your picking and packing in house. When sales grow, a warehouse management system with pick and pack facilities can allow you to scale and fulfill orders with greater accuracy.
Order fulfillment clues you in on where warehouse inefficiencies originate and how to minimize them to improve your fulfillment rates. This knowledge can help you to either pick the picking methods for yourself or a 3PL/4PL provider you can hand picking and packing over to.
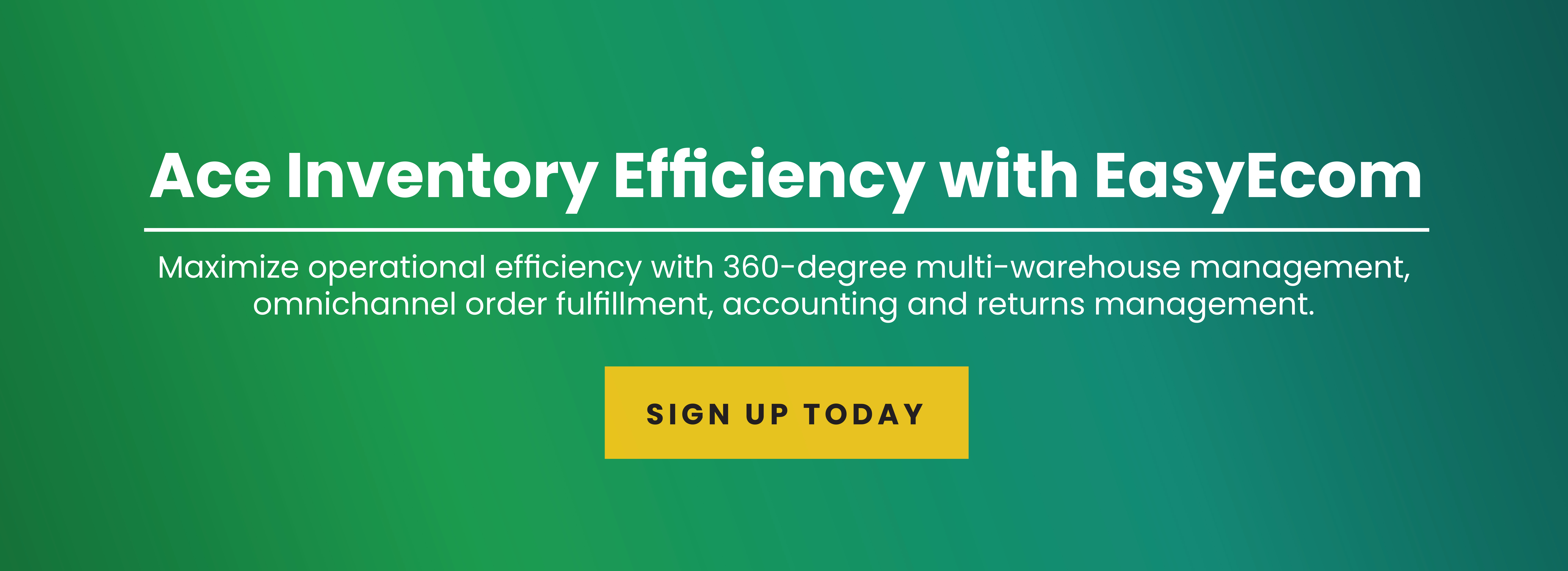