The process of storing inventory or items that are to be distributed to the customers is what we refer to as warehousing. Warehouses can be of different sizes and types based on the requirements of a business. A small-scale business that has just started out can be operated from the owner’s house, a storing unit, basement, or a garage while the larger ones usually rent out a separate area that is specifically meant for storing the inventory.
eCommerce and Warehousing
As more and more customers are shopping online, the eCommerce market is getting competitive and brands have their work cut out for them to stay in the game. As the business grows and you need to fulfill more orders quickly, the need for a warehouse comes into play. Warehousing requirements for an eCommerce business are no different than that of a retail business because the end goal is order fulfillment, regardless of the mode of purchase. Therefore, warehousing is as crucial part as any for an eCommerce business looking to meet customer expectations.
In the beginning, eCommerce businesses might overlook the warehousing needs and focus on marketing and conversions instead. Without a proper warehousing system in place, they can't expect to scale or fulfill orders on time which will result in losing customers.
In the following sections, we have explained the know-hows of eCommerce warehouse management, its benefits, implementation, and best practices in detail.
Let's deep dive into them one by one.
What is eCommerce Warehouse Management
eCommerce warehouse management essentially means keeping track of the stock as it is received, dispatched, and stocked within the warehouse for a business that operates online. This broadly involves receiving, organizing, scheduling labor, stocking, managing inventory, fulfilling orders, etc.
Warehouse management is one of the most important aspects of eCommerce fulfillment. It is crucial for any eCommerce business to get this part right as it makes or breaks a brand. In general, warehouse management in eCommerce dictates day-to-day warehouse operations that include the following:
- Managing inventory and all the equipment efficiently so as to ensure the safety of all goods.
- Demand forecasting
- Maintaining relationships with courier companies for timely delivery of items to end customers
- Scaling warehouse operations with business growth
- Tracking daily inbound and outbound shipments
- Training warehouse staff members to increase productivity and efficiency
Warehouse management directly impacts customer satisfaction. While brands keep looking for new and improved ways to boost customer satisfaction, the basics are lost in the process. The ground rules always remain that “if a customer is unable to purchase the required stock or finds the order process difficult, they will shift to a different supplier. And, that’s why you need to have an effective warehouse management system.
Benefits of eCommerce Warehouse Management
As mentioned above, different types of businesses use different warehousing methods. Small or medium-sized businesses either outsource to 3PL or 4PL companies or maintain a single warehouse/storing facility. A larger business, on the other hand, could be running multiple warehouses simultaneously. Regardless, warehousing has its advantages and it should be handled efficiently and effectively to ensure the smooth functioning of your business. Let’s take a look at some of the major eCommerce warehousing benefits and the key to managing and improving warehouse operations.
Fast Shipping
Customers expect fast delivery and brands compete with one another to deliver just that. For a sizable business, when choosing where to store your inventory, it is recommended to consider distributing it to multiple warehouses across locations. This keeps the inventory closer to end customers, thereby, reducing the time and expenses on the delivery. For small businesses, 3PL and 4PL can be engaged to ensure a faster delivery to the end customers.
Better Inventory Management
eCommerce warehousing can improve the accuracy of inventory tracking and prevent items from any sort of damage. With the right eCommerce warehouse management system in place, this can help you track inventory turnover rates and proactively reorder inventory.
Time-Saving
Time is money and it holds true for eCommerce business in the most literal sense. Without a proper storing space and a system, it will take forever to go through the pile of items that you can better utilize in scaling your business growth.
As your eCommerce business proliferates, you have to make sure that your warehouse is managed efficiently. The day-to-day warehouse management operations ensure that inventory is received, stored, picked, packed, shipped, and replenished in the most efficient way possible. When warehouse operations are efficient, your business could significantly cut operational costs and keep customers satisfied. But, when improperly managed, there is a delay in your orders, workers will not be as productive as possible, and your company loses money and reliability. So, how can you, as a retailer, make sure that your warehouse operations run smoothly?
How to Implement eCommerce Warehouse Management: The Right Approach
Come up with a plan & determine the space you need
Before getting started, you must have a plan to optimize your warehouse space to the best of your potential. A strategic warehouse plan should include diagrams such as floor plans and documentation of resources such as space, labor, and equipment and how each warehouse function utilizes what portion of each of these assets. You will need to have adequate space for the following in your warehouse:
- Unloading, QC checks, labelling
- Stocking
- Forward staging
- Dispatching
- Additional area for surplus, RTO, defected stock
List the Essential Equipment for your Warehouse
The kind of equipment that you need for your warehouse completely depends on the type of products, businesses model, and the number of orders you process on a daily basis. For a typical eCommerce warehouse or fulfillment center, the following basic warehouse equipment is required:
- Storage Equipment- includes shevles, bins, racks, etc.
- Packaging & Shipping Equipment- includes everything needed for assembling, packing, labelling.
- Inventory Management- barcode readers, printers, etc.
- Material Handling Equipment- includes everything needed for loading, transporting, storing, positioning.
Select the right Warehouse Management System (WMS)
Now that you have optimal warehouse space and all the essential equipment, look for a warehouse management system that will help you keep track of all your warehousing activities and automate repetitive operations. In general, there are 4 types of WMS for you to choose from- Standalone, ERP module, supply chain module, and cloud-based WMS. Based on the requirements, you can select any of the above-mentioned systems and start with the warehouse automation process.
We will discuss WMS in more detail later in this article, along with best practices to implement.
Track KPIs
Even if you have a functioning warehouse management operation in place, there is always room for improvement. Warehouse operations managers can improve warehouse performance by defining and monitoring key performance indicators (KPIs) such as:
- Receiving efficiency
- Picking accuracy
- Carrying costs
- Inventory turnover
- Rate of return
- Backorder rate
- Order lead time
These KPIs will help you gain an optimal performance rate. Supply chain technology and analytics should be used to forecast the demand rate. Having excellent supply chain visibility is key to eCommerce operations. During eCommerce events like seasonal sales, there should be adequate inventory and suppliers on call due to the spike in demand. You can monitor trends, of course, and prevent yourself from ordering excess inventory but there is always a possibility of storing items above the threshold. It helps in mitigating potential risks in your warehouse and doesn’t affect your eCommerce rankings or business performance.
eCommerce Warehouse Management System: When to use? Benefits
Deploying a warehouse management system allows your company to optimize warehouse operations, cut on any labor expenses, keep a check on the inventory levels, and maintain its accuracy. Automating your warehouse operations is important but one should be careful about when and how to go about it.
For a larger warehouse with multiple staff members, one of the major challenges is to locate a particular item. With a WMS, this becomes a matter of seconds. Furthermore, a WMS is capable of monitoring product quantities, cycle counting, picking, packing, shipping, and managing multiple locations.
Here’s a checklist for when you need a warehouse management system for your organization:
- You have a large warehouse or multiple warehouses
- You fail to dispatch orders within specified SLA
- It’s challenging to track your shipments and returns
- You find it extremely time-consuming to search for a product in the warehouse
- You process more than 50 orders a day
- There is more than one team member doing the pick and pack job
Benefits of a Warehouse Management System (WMS)
The WMS system integrates the workers, task handling types of equipment, storage tracker onto a platform called warehouse management software. It majorly prevents manual errors by working on system-directed operations of receiving, putaway, picking, and shipping. Let’s look at some of the major benefits of a WMS.
- Complete Inventory tracking
Complete and systematic tracking of the overall stock movement within the warehouse ensures avoid situations like over/understocking or inventory shrinkage. Additionally, item-level barcoding helps with the complete history of a particular item, which is helpful for RTO or re-shipped products.
- Manage Quality Control
At the time of receiving, a detailed QC process ensures that the product inwarded for sale is actually correct. This WMS functionality is particularly helpful when you process a large volume of inventory per day and the chances of defected items flowing in are higher.
- Effective Inventory Planning
A WMS gives you insights into your most and least popular products for any time duration. Based on this data, you can make decisions on what products to invest in and for what amount of time, thereby, helping you with accurate inventory planning.
- Improve Warehouse Staff Productivity
WMS enables different members of your staff to log in to the system under different capacities. Additionally, when they know the exact locations of the items, the pick-pack time reduces significantly.
- Reduce Security Concerns
A WMS keeps the record of all items that are received, picked, and packed within the warehouse. This information can be accessed with specific user logins only, hence, the chances of anyone slipping extra or damaged items are basically nill.
Best Practices for Efficient Warehouse Management
There is no concrete set of checklists for you to manage your warehouse, however, there are some tried and tested practices that come in handy in streamlining warehouse operations.
- Audit your warehouse operations: One of the tools in managing warehouse operations is conducting an operational audit. Auditing your warehouse every year helps you in updating stock and accounting for all products gone missing. Evaluate whether changes need to be made to make it run more effectively. This also helps you in gauging your supply chain performance.
- Implement cross-docking and labeling: Cross-docking is the practice of unloading materials from an incoming vehicle and immediately loading the same items directly onto the outbound vehicles with minimal warehousing interval in between. It helps in reducing the TAT and increases profits and is of course, time-saving. Mostly, the companies in the pharmaceutical sector use cross-docking to save time and distribute their perishable products to the end consumer. Walmart is also known to implement cross-docking for a lot of their items. Labeling also helps in having a fast-moving warehouse. SKU numbers, clear labels, or barcodes can help in the easy identification of your products.
- Implement safe measures in your warehouse: A safe warehouse means implementing regular training and awareness courses. The staff that knows how to use equipment safely and adequately typically keep warehouses running more efficiently and better managed. Safety protocols must be followed sincerely, and danger zones must be marked and noted by the staff.
- Increase staff productivity: Managing a warehouse needs a productive team to make sure orders are not delayed. A warehouse manager can make sure the staff is adequately taken care of and efficiently conducting themselves. Loyalty programs, incentives, and other morale-boosting programs can be set up so that they do not feel burdened. The workers should also be educated and trained correctly to maximize productivity. A lot of brands conduct seminars and workshops for their employees to ensure that their staff is well-trained and informed about the operations.
- Maximize your space: As we said earlier, having proper documentation of your floor plan and warehouse space helps you take care of more inventory. The warehouse should be organized in such a way that the operation flow from receiving to packing is done smoothly. Making use of vertical space and bin locations also helps in maximizing your warehouse space and easy to navigate.
- Track the right metrics: Tracking the right KPIs makes all the difference. It helps you gauge your vendor performance, delivery accuracy, customer satisfaction, and much more. Using data to analyze these metrics are also important. Having a thorough understanding of these numbers is also crucial for the growth of your eCommerce business.
- Invest in a Cloud-based Warehouse Management System: A WMS like that can automate and implement tracking of your day to day warehouse activities. Locating a particular item within the warehouse can be challenging for a large warehouse with multiple staff members. A cloud-based WMS not only solves this particular issue but it also allows different staff members to use the same system in different capacities. Furthermore, it will monitor product quantities, cycle counting, picking, packing, shipping, and even manage stock across multiple locations in real-time, based on the information stored on a remote server that can be accessed with a good internet connection.
You'd be able to make out the most of your warehousing space with the above-mentioned practices, and they work for both single and multiple warehouses. However, when it comes to the latter, there are certain additional things that you should be aware of.
Before opting for multiple warehouses or distribution points, check for the following things.
- Operating costs for opening additional warehouses
- The number of SKUs
- Monthly order volume
- ROI on additional expenses
If these aspects are sorted, you are off to a good start. Now, let’s move on to how you handle multiple warehouses after these are up and running.
Managing Multiple Warehouses
Multiple warehouses give you the benefit of time and utility that can't be easily achieved with a single warehouse. The deliveries to customers get faster, transportation costs are reduced and it provides the business easy accessibility to raw materials and storage.
However, these come with a plethora of operational challenges that might affect the productivity and efficiency of your eCommerce business. Automating WMS with advanced features to assign, redirect, restock inventories on a real-time basis is the most optimal solution. Here is what you look for in a WMS while you have or hope to manage multiple warehouses:
- Cloud-based system
For multiple locations, a WMS that is cloud-based allows you to monitor your inventory from anywhere on a real-time basis.
- Option to set stock level and re-order alerts:
To achieve the optimum level of inventory management, it is important to identify the maximum level, minimum level, average level and reorder level for each SKU per the warehouse. This helps in minimizing the cost of overstocking and out-of-stock situations where you lose out on sales.
- Inventory Forecasting tool:
The inventory forecasting tool is fairly vital to understanding the pattern of stock movement. It is not necessary to maintain each SKU in every warehouse owned. Have backup plans for each aspect of inventory management.
- Make Warehouse wise inventory record:
While keeping records of the available inventory, it is always advised to keep the record warehouse-wise so that any overbooking can be redirected to the available warehouse for successful order fulfillment.
- Automate Warehouse Management
Automation of each warehouse includes cycle count, serialization of stocks, quality check, put away option, shelving, barcode scanning, PO generation, gate pass, and a lot more.
- Identify Stock Demand segregated Geographically
Multiple geographic locations will have different demands, choices. The Omnichannel solution must have an excellent data analytics tool to provide a report on the demand pattern on the basis of warehouse location and season of sale.
- Have multiple supplier management for high demand products
For fast-moving items are items, there is always a concern of shortage that might go unnoticed. Therefore, it’s always safe to have multiple suppliers who can constantly fulfill high-selling items in the stock.
- Audited stocklist Report:
The inventory Count feature in a WMS is used to avoid unexpected stock shortages. All these reports on the dashboard must reflect data that will help you understand your inventory status on a regular basis across the warehouses.
Easy Warehouse Management for eCommerce Sellers
A lean and efficient warehouse keeps your eCommerce business running efficiently and does not hinder your supply chain. Each action should support the organization’s goals while being aimed at increasing productivity and safety, optimizing space, reducing costs, and top-notch customer service. A perfect mixture of automation and manual labor can make managing your warehouse a piece of cake.
EasyEcom’s centralized inventory management solution comes with an advanced state-of-the-art WMS platform which has built-in provisions to handle bulk orders and accounts reconciliation tracking for all your warehouses. Our WMS Solution seamlessly integrates with all the major sales channels that offer transparency in inventory movement.
Some of the features that our WMS offers include:
Inventory forecasting- The system suggests you with inventory items you need to buy and in what quantity. This ensures your warehouse has optimal stock available to timely fulfill orders.
Supplier and purchase order management- You can manage POs sent to multiple vendors from a single dashboard. Once goods are received at the warehouse you can record Goods Received Note (GRNs) to keep track of your available inventory. While receiving goods, the system also provides you with the functionality to record quality status and assign shelves to products. This helps your warehouse team easily pick products during order processing.
Barcoding- The system provides you with an option to record products received at SKU level and Item-level. Item-level tracking is especially helpful in case you deal with a large inventory line or expensive products wherein tracking individual units is required.
FIFO & FEFO Inventory Management- The system’s strong perishable product management system ensures you only sell products that have a long shelf life remaining. For non-expiry products, the system follows the First-In-First-Out method while assigning inventory for order fulfillment.
Advanced Shipping Rules- You can prioritize carrier partners and define shipping rules based on which the system automatically assigns your orders to the logistic partner.
Order Routing- You can set order routing rules in the system to ensure that your order is directly routed to the warehouse of your choice.
User Roles- You can define multiple user roles in the system to ensure that your team members have access to the required information on a real-time basis.
We recommend that you connect with our solutions expert for a full demo. You can also sign up for the same here.
Before we wrap up, here is a list of key WMS trends your brand must factor in:
eCommerce warehouse management is as important as marketing, conversions, or any other supply chain operation for your business. If you are doing it right, you take a major leap towards an optimized supply chain. Here, we have covered the benefits, processes, and best practices for doing it effectively. In the next one, we will take up the types of WMS you can choose from for your eCommerce business.
Are you looking for an omnichannel inventory management solution with integrated B2B order management for your eCommerce business? Drop us a line at care@easyecom.io or directly sign up for a demo here.
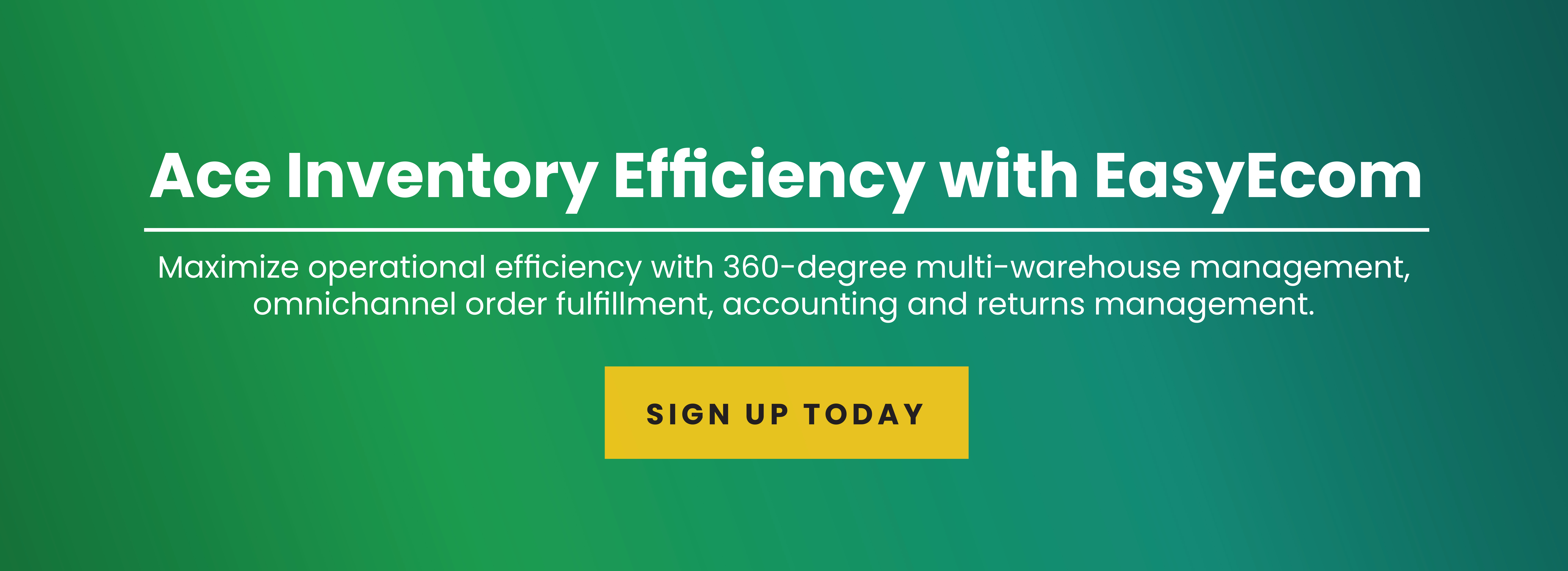