The customer base is expanding, sales are peaking and order volume is rapidly rising.
Everything, in short, indicates that your eCommerce enterprise is right where you want to be. But something still doesn’t sit quite right. Someone from your operations team reports irregularities in item quantities which brings up two questions.
When and how did some of them go missing, and more importantly, why did the difference in inventory levels take so long to be discovered?
Vendors default to using SKUs to track their inventory because it suffices in providing high-level views into the same product line in terms of available quantities, sales etc. serving multiple purposes of tracking, omnichannel selling and accurate sales data. However, it’s a different ball game with in-demand, specific categories like consumer electronics, defense and automotive equipment and medical supplies that require more granularity beyond what SKUs are capable of. That’s when serialized inventory enters the picture.
Serialization helps to track individual units at any warehouse, even if the products share the same SKU. This enhances traceability and blocks a defective unit from fulfilling an order without affecting the other units. All these satisfy the overarching goal of streamlined warehouse operations without wasting efforts and resources.
In this post, we’ll look at serial number inventory tracking and clear up the confusion surrounding barcoding, serializing and more. Read on!
What is Inventory Serial Number Tracking?
Inventory Serial Number Tracking is an inventory system that tracks individual units from the time it is produced by the manufacturer to its sale. Typically, manufacturers stamp or roll the serial number onto the product to prevent it from being tampered with.
The unique identification code or ID helps to know which unit was sold, when and to whom. In other words, it creates a trail while the items move through the supply chain and change multiple hands, with each involved partner having access to the same information on their systems. Serialization facilitates accurate inventory assignments and holds the right person(s) accountable in cases of theft, loss, damage and returns.
For example, in situations where a product is marked as returned to the warehouse but has not yet been delivered, manufacturers can isolate those products by their serial numbers and raise disputes or file a claim with the marketplace or courier partner.
How are Serial Numbers different from SKUs?
At first glance, SKUs, barcodes and UPC(Universal Product Code) all seem to be talking about the same thing. And they all enhance tracking and traceability. But choosing one over the other depends on the sector, industry type, size and regulations or laws that the business should comply with. In some cases, they complement each other when lumped together, with the SKU identifying the type of product and serial numbers specifying the unique unit it belongs to. We’ve listed out a few key differences between SKUs and Serial Numbers;
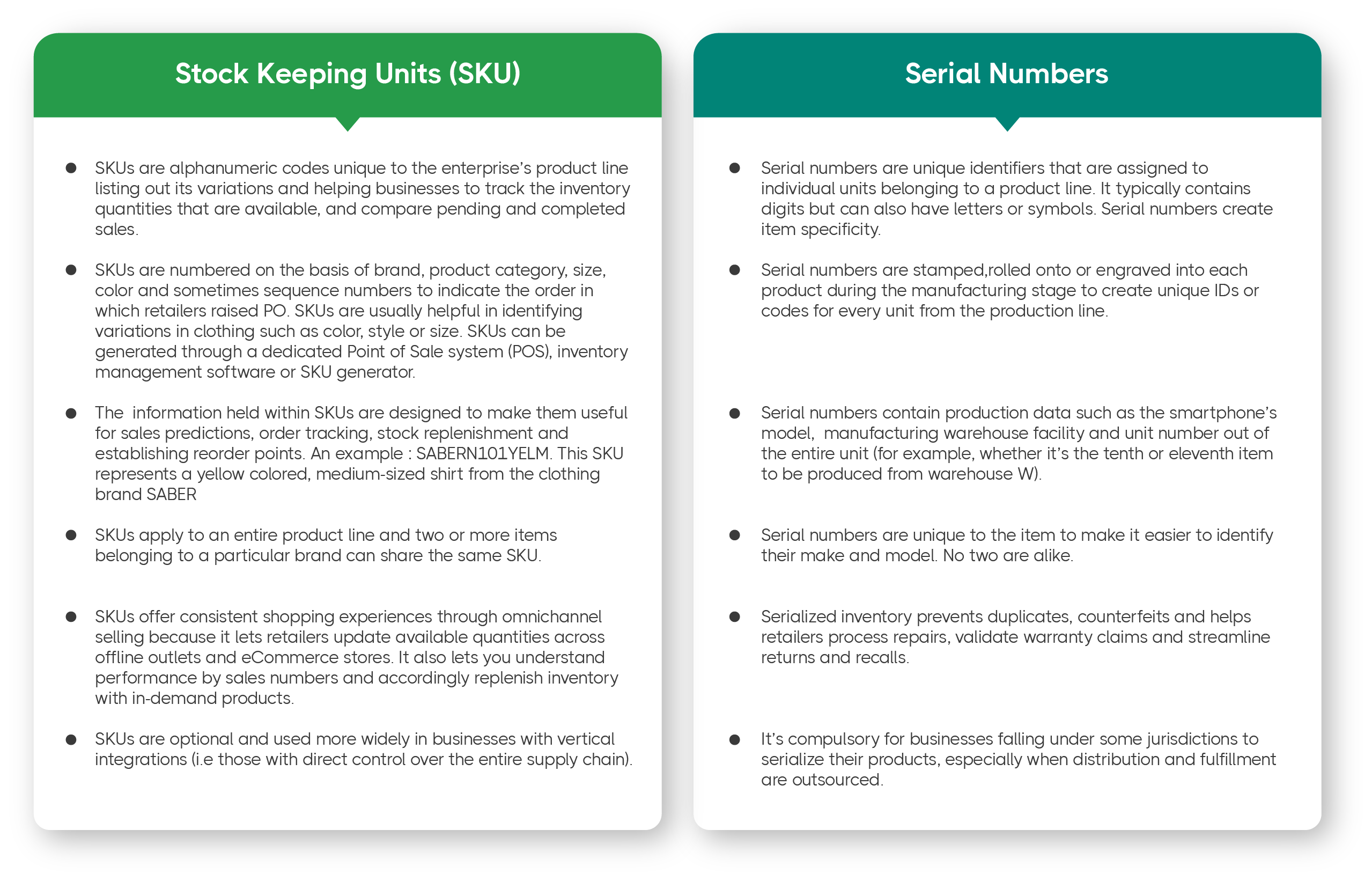
How does Serialized Inventory Tracking Work?
Serial inventory tracking is crucial to industries like healthcare, petrochemical equipment and devices where expired, counterfeited or faulty products can even endanger lives. It provides enterprises with granularity that minimizes exposure, insuring them against inflated returns and recalls costs, potential theft, damage and or loss. Serial tracking typically flows in the sequence listed below;
- The manufacturer assigns a unique serial number to each item, usually through barcoding or RFID tags, which is then recorded into the inventory system.
- All serialized items are sorted into units and shipped to the distributor or retailer, who then scans the items to enter the serial number into the inventory system.
- The customer is sold the item, and gets a receipt for it which includes the serial number.
- The customer should provide the serial number to the retailer or manufacturer in cases of warranty claim filing.
- The manufacturer or retailer uses the serial number to fetch the item’s history, crosscheck warranty TnC(terms and conditions) and period before reverting with the best course of action.

Why is Serial Number Tracking Important?
Some industries require it, such as healthcare device and lab equipment manufacturers or defense and automotive machinery. But serializing inventory poses numerous advantages to other high-value, expensive and large sized omnichannel eCommerce enterprises, too.
When you serialize inventory, there’s less margin for error and delay. Workers can find what they’re looking for and confirm their identity confidently and rapidly, which drives up the overall inwarding efficiency. Retailers can also confirm that they've received the right products from all the manufacturers that they're working with. If any unit is found to contain faulty or defective pieces, those items can be separated and locked away to prevent accidentally mixing them in with undamaged products. The retailer or distributor can then contact the concerned manufacturer and arrange to send them back. This saves costs associated with returns and refunds and ensures that only those products deemed fit for sale end up fulfilling orders.
A detailed inventory record keeps everyone on the downstream(i.e. demand) and upstream (i.e. supply) sides of the supply chain informed of the sequence of item movements belonging to a specific unit. This makes it easier to match quantities, report differences and trace mismatches.
Even in instances where assistive intervention is required, customers who provide their product’s serial number can instantly display all relevant details to the support staff, facilitating quicker query resolution. If a return or recall (a sub part of returns management that necessitates all units going back to the manufacturer with immediate effect) , stores have all the information needed to smoothen the process.
Do Serial Number Tracking and Barcoding Mean the Same Thing?
At first glance, serial numbers, SKUs, barcodes and Universal Product Codes (UPC) all seem to be interchangeable terms that accomplish the same goal. But there are subtle differences. When used together, serial numbers and barcodes improve inventory management, warehouse efficiency and asset tracking.
Serial number tracking is that process which allots unique codes to each and every individual item in a product line, meaning that no items from the same manufacturer are alike. Serial numbers can be a numeric sequence or slightly more complex with the usage of barcodes and RFID tags.
Barcodes can be thought of as a subset of serial numbering. They are machine-readable symbols that can be seen on labels, invoices, sales receipts etc. Barcode scanners can pick up the serial number and instantly verify details such as manufacturer, warehouse, unit or lot number and production date, helping to ID the product and establish manufacturing authenticity. Barcodes are used at offline outlets by cashiers during checkout, which is why the serial number can be seen even on receipts. It can even indicate which store location the item was sold from! When used together, serial number tracking and barcodes create a robust tracking system.

Five Post-Sales Use cases of Serial Number Tracking Systems
Anti-Theft
When high-value items are stolen, serial tracking can help law enforcement personnel nab the culprit and recover the item. The original ownership can be verified using the same number to confirm the identity before returning the item.
Inventory control
Serialized inventory contains expensive categories, where both quality and quantity matter. You want exactness in reorder points to control inventory costs and prevent excess inventory from being stored carelessly. More importantly, serializing reduces the amount of time workers would spend looking for specific items or spare parts. All they’d have to do is simply run the serial number through their systems, helping to track down the warehouse it’s sitting in currently and which warehouse it was moved from.
Product Recall
Recalls are a messy and costly affair and maximize the wrong kind of exposure to an enterprise. No matter who is really at fault, the finger of blame will point at the brand, questioning its quality control and compliance measures. Assigning serial numbers to both parts and finished goods can minimize the hit to business reputation, especially for manufacturers with factories spread worldwide. When you work with several suppliers, it’s probable that one could have sold faulty pieces to distributors or directly to customers.
Instead of recalling every product, you only need to recall a particular piece or batch that came from the same source. The serial code on returned items can confirm that the item was made in the same production run, and can be separated efficiently for further evaluation. This minimizes the loss your enterprise would have had to absorb from refunding the order value.
Compliance
Serial numbers are a legal requirement that electronics, vehicular and expiry-sensitive device manufacturers should comply with to aid in compliance efforts. For example, all cars have a Vehicle Identification Number on their chassis to indicate manufacturer details, model and make to identify the car in accidents, broken laws or getaways.
After-Sales Services
Serial number tracking authenticates warranty and zero-cost repair claims, expediting after-sales services. Serial tracking allows you to source the right replacement and match it to the right product to service it without compromising the original quality.
What does the future hold for serialized tracking?
Hybridity is the future of retail, from buyer journeys to last-mile logistics. Looking at inventory control from multiple perspectives, serialized tracking supports an eCommerce enterprise’s goal of driving seamless customer experiences.
How?
By providing data instantly that you can trust. Unique serial numbers offer micro-level transactional history for thousands of individual items no matter where or when it was produced or shipped from. This means that there are fewer and rarer incidents of disingenuous products and invalid claims, which is particularly important if you retail in high-end luxury goods or sensitive equipment.
FAQS
What are some Common Challenges associated with serialized tracking?
1. Data Management -How many oyster shells would you have to shuck before finding a pearl? That’s how it feels to have an ocean of unstructured data. The key is to use a dedicated inventory management system that sifts and sorts through serialized data so that information integrity is consistently maintained.
2. Infrastructure - Serialization tracking requires additional expenditure on device installation, training and deployment, such as handheld terminals, barcode scanners etc. Businesses will need to ascertain if their current budget fits or the extent to which it can be stretched in preparation for serialization.
3. Training - Warehouse staff need to get used to handling devices and require adequate training to implement serialized tracking effectively.
4. Cost - Serialized tracking can be an unneeded extravagance for small and medium-sized businesses with fragmented processes and limited resources. What starts out as an efficiency upscaling tactic will then turn out to be a financial liability. Businesses wishing to implement serial number tracking need to do a cost-benefit analysis to determine if their product category is worth serializing.
Should MSMEs consider serializing inventory?
SKUs are generally sufficient for smaller enterprises because it provides just the exact and right amount of information needed to manage inventory. UPCs and Serial numbers are more applicable to manufacturers for individual item-level tracing.
Does serial number tracking pose a privacy concern?
In some cases. For example, consumer electronics manufacturers of items such as USB sticks or hard drives, require customers to register the product on their website for warranty claims. If the website gets hacked, these and other customer details can fall into the wrong hands. ,
Are SKUs and UPCs the same thing?
No. While SKUs are used by individual retailers (omnichannel or offline), Universal Product Codes or UPCs can be used by different retailers in the same product category located in different places. UPCs are usually 10-12 digits long and correspond to a barcode, with the first 6 digits indicating the company owning the intellectual property rights. UPCs are more universally recognizable because they are regulated by GS1, an international non-profit outfit.
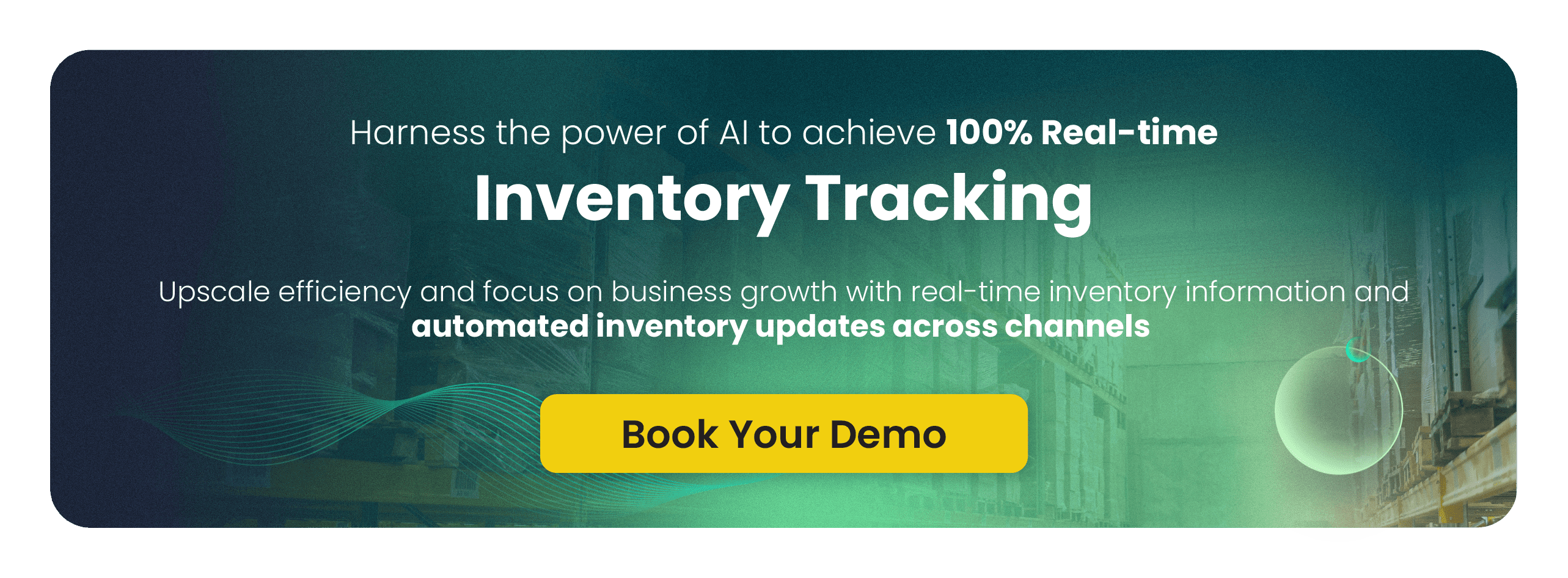