The global warehouse management market size is expected to reach $21.6 billion by 2027. As economies around the globe make a gradual recovery from the economic recession, warehouses, distribution and fulfillment operations are rapidly evolving to keep up with the growing demands of a population seeking instant gratification. It starts with scaling up warehouse efficiency due to the fact that the maximum activity(and maximum room for error) lies inside a warehouse.
In this read, we’ll look at the key trends surrounding warehouse operational efficiency with tips to upscale it.
The Key trends shaping warehouse operations in 2023
RPA
Automatic storage and retrieval systems (ASRS) are not the newest kid on the bloc, but are rapidly being adopted by large B2B businesses for the scalability and precision they offer. In fact, by 2023, 75% of warehouses are expected to use some form of automation. Besides claw pickers, forklifts and sensor-built conveyor belts, warehouse workers are using wearable tech, handheld devices and mobile barcode scanners to allow for freedom of movement while minimizing risks to personal safety.
Flexible warehousing
Flexible fulfillment enables businesses to respond to seasonality and uncertainties. It is useful in stepping up during emergencies which generates demand for specific items. Take the pandemic situation for example, which necessitated the supply of lifesaving and cautionary equipment such as gloves, masks and outfits.
The rise of micro fulfillment centers
Micro Fulfillment Centers or (MFCs) are the answers to an eCommerce seller’s prayers for quick and efficient deliveries. As smaller centers that are in closer proximity to a customer’s address, MFCs can fulfill orders from multiple retailers and brands while costing companies less. But the biggest flex for MFCs is that they can be more easily automated as they take up less space, allowing them to respond to a rapidly changing market.
Supply chain visibility with the connected warehouse
As supply chain leaders move away from clipboards to smart scanners and handheld devices,AI-powered warehouses are leaving an efficiency mark in several areas, most noticeably in collecting and processing information concerning stock quantities. Supply chain visibility is now end-to-end with a cloud-based warehouse management system that gives you unconditional visibility and insights to apply efficiency improvements. You can lock and store critical numbers regarding inventory, orders, customer details, assets utilized, returns and charges or claims filed, ensuring there’s no breach or leak that compromises organizational integrity.
Sustainable warehousing
More and more consumers are environmentally conscious and taking steps to minimize the adverse impact their actions leave on the earth. Therefore, evolving consumer demands are centered on sustainability, encouraging companies to rethink their approach to sourcing, packaging and transportation. Several brands disclose their post-sales CSR and have found a niche with a steady or predictable demand. Even the switch from linear to circular supply chains aligns with companies aiming to be transparent with their customers about recycling measures that they are undertaking. Internally, measures supporting the green revolution include use of energy-efficient systems like solar panels and biodegradable alternatives at manufacturing hubs.
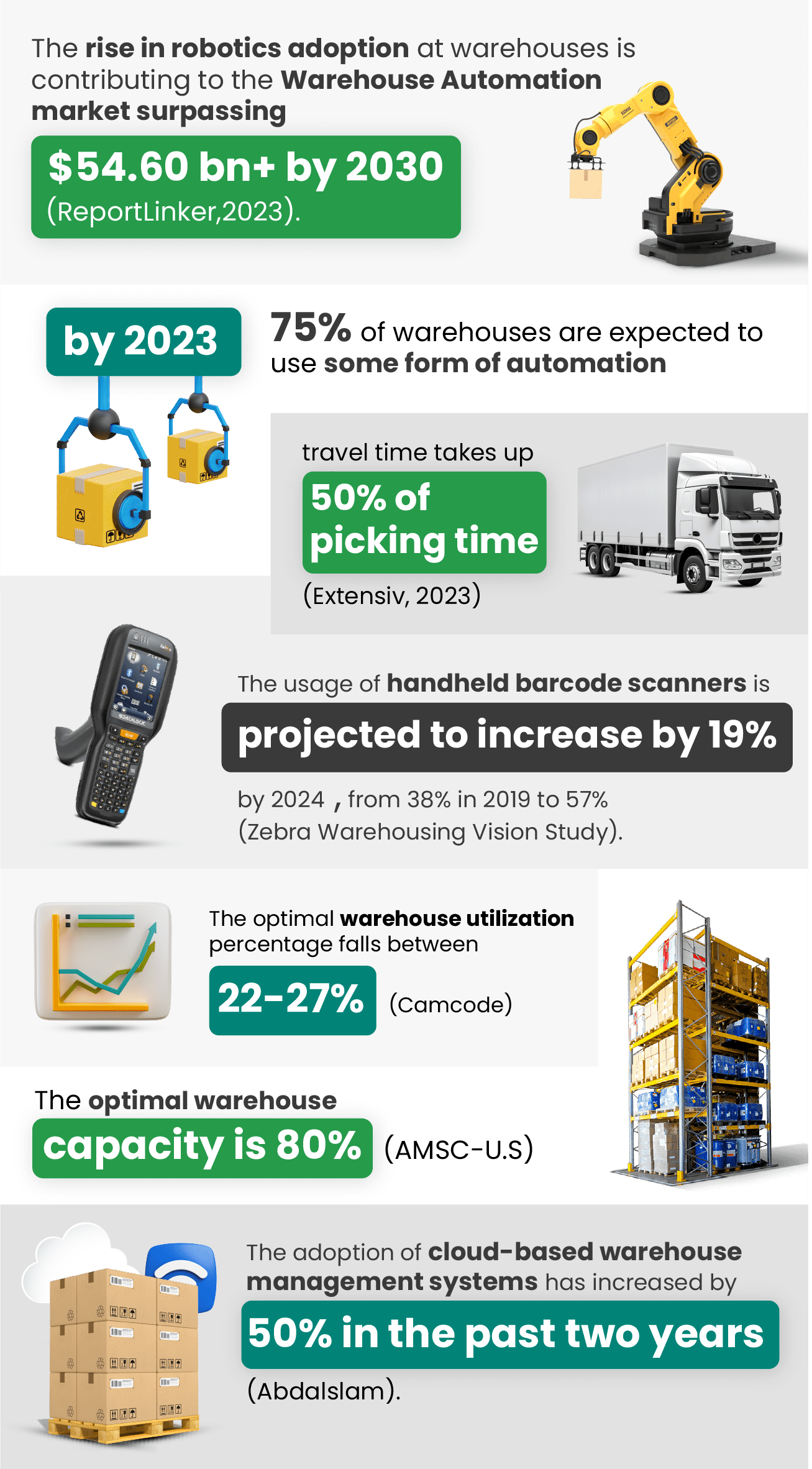
Hacks Worth Trying For Improving Warehouse Efficiency
Perform a warehouse audit
You cannot measure what isn’t tracked, and you cannot improve that which isn’t being measured. A warehouse audit can remedy this by closely examining existing workflows, from the receiving end of how much stock is onsite and available to the number of shipments readied for fulfillment. It will look into the in and outflow of goods, investigate supply chain inefficiencies and benchmark performance against the parameters of;
- 100% inventory accuracy
- Streamlined order fulfillment
- Optimal space utilization
- Maximized workforce productivity
- Cost-effective operations
Practice strategic resource utilization
The biggest time suck (and money pit) in and around a warehouse lies in not utilizing your human resources right. In fact, travel time takes up ~50% of picking time, resulting in you paying your runners to walk rather than pick. Having them focus their efforts in the right areas raises productivity, boosts morale and saves the legwork.
While newly oriented hires can file orders, putaways (shelving) are best handled by seasoned workers who are familiar with products and how the bins and shelves should be stocked. Putaways are crucial in warehouse management in that there’s an electronic record of updated inventory levels that can go back up on sales channels as available or stocked products.
Through an AI-driven eCommerce solution like EasyEcom, warehouse workers can shelve items with precision by returns and cancellations. The subsequent reports on the Putaway activity and item-wise cancellations record the initial putaway bin,location, and putaway status with timestamps to ensure that the inventory quantity is updated in real-time.
With easy access to these details, the warehouse manager can identify and prevent shelving delays to ensure sales are made.
.webp)
Use forecasting to plan inventory
As they say, forewarned is forearmed which rings true for warehouse managers.
With forecasting modules, sellers can plan inventory and get shelf-wise stock statuses that reflect actual availability, ensuring customer expectations can be met. For instance, the Inventory Planning By Days report can indicate the number of items that a seller will need to reorder from their supplier within a certain timeframe. It looks at historic data and generates a view of the remaining balance in your inventory against the orders received in the previous month, allowing you to achieve an exactness in the quantities to be ordered again. This is a cost-saving measure as you’re neither paying beyond the required amount for procurement, nor are you stuck with surplus stock that can easily slip into slow-moving inventory if demand dips.
Stock reports are also an efficiency improvement measure where the seller can recheck product information and see how many units received have been blocked for an order. Such comprehensive analytics prepare you for seasonal demand associated with thematic holidays and events. The best part about forecasting is that it takes care of things that you wouldn’t have previously thought merits consideration, such as staff shifts, space utilization and storage optimization!
Make use of proper and informative labeling
The more information a label contains, the better the chances of correct, damage-free deliveries. Labeling informs warehouse workers of the level of carefulness expected of them when handling the movement of goods and makes it easier for workers on receiving docks to cross check information before shipping. All receiving labels should contain basic details such as the Purchase Order (PO) number, supplier name, quantity and product code.
Perform cycle counts
Inventory cycle counts should involve a digital verification of manual counts to ensure the ledger data matches. If it doesn’t, you have the opportunity to investigate and rectify rather than let the error stretch to the outwarding. Regular cycle counts can audit stock and save you costs.
The Inventory Record Accuracy, or IRA, is a formula for knowing the accuracy percentage of inventory cycle counts which is
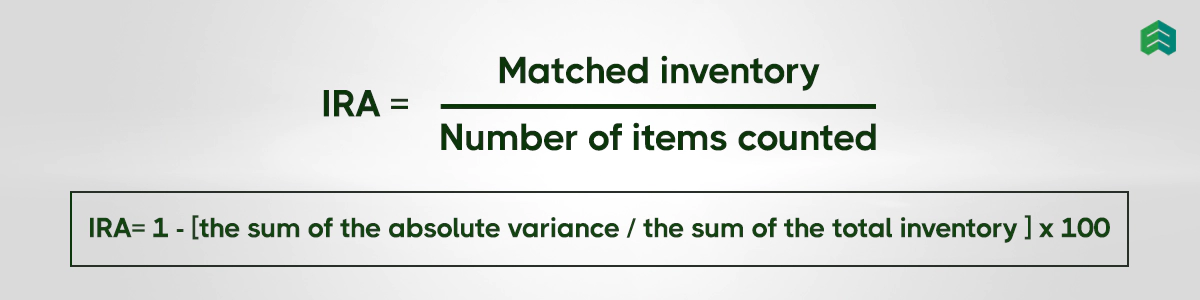
For example, if the manual count turned up 200 and the system counted 350, the IRA will be 85%. This figure should ideally be 100%, and over time, the number of products, counters and counting frequency can determine how often cycle counts should be performed.
We would recommend not waiting till the end of year to do this. Sync up a time across warehouses to perform the digital count in shorter and quicker iterations so that distributed teams are made aware of the data recorded. Through EasyEcom’s dedicated Warehouse Management App and handheld terminal devices, workers can perform cycle counts and achieve 99.99% bin-level inventory accuracy from the comfort of a mobile device.
Do ABC analysis
The ABC analysis in inventory control prioritizes inventory items by sectioning them according to their value and sales performance. Products falling under “A” sell best while “C” holds low-performing products. The ABC analysis runs on the 80/20 Pareto principle where 80% of revenue comes from the top 20% of items. By identifying items that sell best, those can be put in a staging area which is more accessible to pickers and picking robots, making for easier and quicker picking. By pushing underperforming items to inaccessible areas, there are fewer chances for error and transportation time can be cut down by as much as 60%.
Track and manage damage rates
Items returned back to the origin or vendor on account of damage need to be tracked in order to determine at what stage the damage might have occurred. Consequently ,preventive measures can be taken. With pending and confirmed returns reports that are readily available on the EasyEcom system, sellers can monitor and minimize returns. They can redesign packaging and switch to sturdier alternatives. The costs for doing so will need to be included at the time of renegotiating supplier contracts, so that all goods coming from their end are uniformly and soundly insulated from damage. If the damage is contained to packaging alone and the product is still usable, it can be returned to the shelf and restored to inventory to go back on sales channels.
Reduce touches
Pick and pack processes need to be automated to improve warehouse efficiency. By reducing the number of touches, workers can be saved from unnecessary physical risks and injuries and are freed up to spend their time elsewhere on more productive tasks.
Track Fulfillment
Fulfillment indicates a seller’s success in meeting their customers’ expectation of timely, damage-free and precise deliveries and is an important metric for Service Level Agreement (SLA) adherence. With SLA reports, you can drill down to process inefficiencies, discover where they are happening and why, and ultimately make corrections to minimize negative feedback and complaints.
Use barcode scanning
According to a Zebra Warehousing Vision study, the usage of handheld barcode scanners is projected to increase by 19% by 2024 , from 38% in 2019 to 57%. While only 59% of supply chain decision makers reportedly use barcode scanning in addition to the RFID tags for inventory management, cross docking and picking, things are starting to look up, with this estimate rising to 97% by 2030. The accelerated adoption reflects the understanding supply chain experts would have obtained in due course from using automated capabilities. When it comes to order processing and fulfillment, barcode labels on products and pallets can immensely improve warehouse productivity by informing personnel of what is available by location and quantity.
Leverage AI-eCommerce SaaS
An eCommerce enabler that unifies sales channels across offline and online can enable you to track inventory, orders, warehouses, payments and shipping in a single place. Instead of going in and out of several tools to accomplish concurrent tasks, you can streamline warehouse management and ensure orders are routed to the right warehouses by priority, distance and location. Sellers can also keep a close eye on the movement of goods and understand the circumstances behind delays and errors that can give rise to defective or damaged shipments. By staying proactive in identifying and minimizing risks, brands and wholesalers can keep their customers happy with timely, accurate and error-free deliveries.
Track inventory levels to avoid overstocking
In a demand and supply economy that impacts pricing points, sellers should expect their stock levels to rise or dip accordingly. But in the interest of growing sales, sellers often make the mistake of inflating product availability and then scrambling to overstock to make sure that orders can be accepted. Overstocking warehouses is a shortsighted and costly measure, because while it makes sure you do not run out it does present a headache later on. It takes up floor space and invites higher and longer maintenance costs. More importantly, if demand falls, you’re stuck with excess inventory that defaults to slow moving and wind up having to offload it at a considerable markdown in the later months, and this is assuming there’s demand for it then.
Therefore, use the right reports for data on updating your inventory by quality and performance. For instance, the inventory aging report can inform you of the units available in the current inventory and point out shortfalls that can be corrected. With accurate tracking, you have product sufficiency for order fulfillment. You can also use the concept of endless aisles or infinity aisles to extend your inventory to fulfill orders placed in-store. This way, even if you’re running low on requested items, you can know when to replenish strategically.
Sync packing and shipping stations.
The order in which goods move throughout the warehouse is that it goes from pickers to packing stations and then placed on the conveyor belt to the shipping station. The two stations can be in close proximity to add velocity to the tasks. Which result in
- Consuming less labor.
- Streamlining the fulfillment process
- Shortening and optimizing distances which frees up space and accommodates a newer influx.
Use cross-docking to stay time-efficient
Cross docking essentially takes out the storage component by unloading products from a truck and reloading them back onto outbound trucks. There are two components to cross docking i.e., pre and post-distribution. The supplier and retailer benefits from more time to decide where their goods should be shipped, depending on whether the order was placed online, or offline and by looking at point of sale trends. The result is fast moving products. Instead of emptying and restoring shelves repeatedly, there is a staging area close to the loading dock where products can be prepared for instant retrieval and dispatch.
Use velocity-based layout
When we picture warehouses, we imagine rows going into infinity. Most distributors group products from the same manufacturer for easy identification or group them by popularity of combo orders. A WMS system can help reexamine the effectiveness of these methods and suggest an update to the layout to make it easier on your warehouse team to identify, verify and expedite fulfillment processes. In a velocity-based layout, the best selling or frequently picked product is placed closer to loading areas while least selling products are placed further away. The zone in which these popular products are placed is called “The Golden Zone” because the products are right where they need to be.
Optimize space and storage solutions
If cost-saving measures are your priority, then it’s time to make the best use of the space that’s available rather than expand capacity. For example, companies can use vertical units for stacking products and use picking equipment that can access these without difficulty.. Grouping can also effectively save costs by clubbing products that sell frequently in high volumes or by seasonality. This can help you identify how to make picking easier for both humanl and robotic labor.
FAQS
What is optimal warehouse utilization?
Optimal warehouse utilization refers to having sufficient room for all warehouse activities across picking, packing and shipping to ensure no space is wasted. Don’t confuse it with warehouse capacity, which is the warehouse space utilized expressed as the percentage of the total warehouse space available.
Determining warehouse levels starts with calculating the total warehouse size which can be computed by
- Finding out what the facility’s total square footage is minus non-storage areas like office/cubicle spaces.
- Multiplying this by the warehouse clear height which is the distance from the warehouse’s finished floor to overhead objects.
Next, the storage area size needs to be calculated by
- Multiplying the length and width of the racks by the height of the highest load in that area.
[PS: the nonuniformity of the highest load throughout the warehouse may cause the height to differ accordingly, in which case they will need to be added up).
- This is the cubic volume, i.e. Potential storage space based on the current setup.
As a final step, the potential storage area needs to be calculated which can be obtained by dividing the previous two numbers and multiplying the result by 100. The ideal number is between 22-27%. The percentage going below 22% is a sign that the aisle width and rack locations can benefit from spatial improvements.
What is the best way to improve efficiency in a warehouse?
1.Order Composition
Order aging tells you how long an order is sitting at your warehouse waiting to be shipped. Order composition by cost and time/item can indicate the time it takes to get products out the door. If the size of the order increases, costs and time decrease inversely because workers spend more time on the floor than on dispatching the item. By allowing your warehouse team to batch orders and work on several small orders at a time, more processing gets done.
2. Warehouse Layout
Improvements made to how space and layout is utilized has a direct consequence on warehouse efficiency levels. The amount of legwork is reduced by routing the team to the shortest paths and to staging areas where quick-selling items are placed..3
3. Methodology
Given how it’s the smaller steps that usually eat up more time, the right methodology addresses smaller inefficiencies first so that they don’t escalate.
What are the essential KPIs to measure warehouse efficiency?
The extensive list of warehouse efficiency KPIs comprises 21 metrics which are summed up here under different sections as follows;
- Inventory
1.1Inventory accuracy
1.2 Inventory Shrinkage
1.3 Carrying cost of inventory
1.4 Inventory turnover
1.5 Inventory to sales ratio - Receiving KPIs
2.1 Receiving efficiency
2.2.Cost of receiving per line
2.3 Receiving cycle time - Putaway KPIs
3.1 Accuracy rate
3.2 Putaway cost per line
3.3 Putaway cycle time - Order management KPIs
4.1Picking accuracy
4.2 Total order cycle time
4.3 Order lead time
4.4 Backorder Rate
4.5 Fulfillment accuracy rate
4.6 On-time shipping rate
4.7 Cost per Order
4.8 Rate of returns
.webp)