Inventory shrinkage means the difference between the physical count of inventory from the total inventory that’s recorded in the official company records.
Inventory shrinkage is a real phenomenon and affects every single retail business on the planet. If not managed on time and with a proper systematic approach, it can prove to be deadly to the company's bottom line.
These differences might be due to various reasons ranging from natural causes or managerial errors, internal theft, shoplifting, or inventory damage, or disposal or loss of inventory with no record. Whatever the reason there is a discrepancy referred to as inventory shrinkage which needs to be accounted for to reconcile the accounting records with the physical count.
Needless to say, this loss of goods directly affects your profit margins.
In this article, we will learn about the reasons for inventory shrinkage and how to prevent them from hampering your business.
Let’s start first with how to calculate shrinkage.
How Inventory Shrinkage is Calculated
As per the accounting rules, the shrinkage should always be marked as an expense in the accounting period in which the shrinkage occurred to match it against the revenue earned during that period.
Check your company's records to determine the value of inventory that you should have in stock based on prior inventory totals and the value of goods sold. This is the book value.
Total the actual value of inventory that you have in stock. This number may be different than the book value because of losses, damaged goods or theft.
Subtract the actual amount of inventory from the amount that you should have according to your financial records.
Let’s consider Mirage Enterprises for example, they have listed $15,00,000 of inventory in its records. After conducting an inventory audit and calculating that the actual amount on hand is $14,00,000. The amount of inventory shrinkage is therefore $1,00,000 ($15,00,000 book cost - $14,00,000 actual cost). The inventory shrinkage percentage is 6.67% ($1,00,000 shrinkage / $15,00,000 book cost).
Another example is if the inventory records of a retailer report that 5,000 units of SKU A are on hand, but a physical count indicates that there are only 4,925 units on hand, there is an inventory shrinkage of 75 units.
A different type of Shrinkage can be referred to as the loss of raw materials during a production cycle. For example, while baking food items the baker will experience shrinkage throughout its production process due to ingredients left behind with the utensils as well as due to evaporation. This is termed as spoilage or waste as well and it can be occurred due to normal or abnormal circumstances.
Now let’s understand what causes the shrinkage.
Causes of Inventory Shrinkage
Shoplifting
You can define shoplifting as when a customer leaves a store or supermarket with more than what they paid for. This constitutes a majority chunk of the inventory shrinkage. The use of CCTV cameras, RFID, Chips, Tags can reduce the shrinkage to some extent.
Employee Theft
Employees are expected to be the people resisting the shrinkage but some employees think otherwise and steal from the employer. The reasons for stealing varies from being greedy to taking revenge on trying to get compensated for being underpaid/underappreciated. This is difficult to track as being the insider they are aware of the loopholes in the system. They can cover up it easily and pass this off as an accident. Proper security systems in place can help prevent this. On top of that, a deeper introspection by the management needs to be conducted if this a frequent event in your company. There might be a general sense of dissatisfaction causing employees to do such a thing, to begin with.
Administrative Errors
With the emergence of digital methods to record-keeping and different warehouse management software, human error has decreased many folds. But it is still one of the major reasons for shrinkage. Consider a situation where a particular SKU is ordered 1000 pieces and while making the entry in the record book the clerk has entered it as 10000. When you conduct an audit of the warehouse, the missing items as per record will be 9000. This will completely jeopardize your inventory record keeping. Some other reasons can be pricing mistakes, accidental reorders, missing zeros as well as left-out decimal points. You need to count and recount the inventory even when the business relies on automated systems.
On top of that, a systematic approach to inwarding where an automated QC is performed based on weight or other factors can be conducted along with manual QC.
Supplier Fraud
When a product changes hand, it becomes essential to keep a record of the stock every single step. There are chances of the theft happening during transit between two warehouses, loading, and unloading. So every time inventory leaves or enters the premises, it should be counted and recorded appropriately.
A gate pass system is required for inter-warehouse transfers to avoid any miscommunication of quantities transferred. In the case of supplier fraud, warehouse inwarding team should be able to catch these while doing the GRN (Goods Received notes). GRN details compared against the purchase bills should help find the issues if they exist.
Unknown Causes
Sometimes, the inventory may disappear off the shelves and cannot be matched to any of the other causes of inventory shrinkage. Unknown causes represent a significant percentage of total inventory shrinkage. A company should have an allowance for such a thing as well, especially in large organizations.
Natural or Accidental Damage
Sub-standard storage areas and unskilled workers make the company take a hit due to inventory shrinkage. Natural calamities can ruin stocks. Even a normal roof leak can cause severe damage to the inventory. If water-logged goods are there it gets damaged due to improper maintenance of the warehouse. Apart from these human errors, natural calamities like violent storms can destroy the whole warehouse. Again, the chance of goods getting damages arises while the shipping process, or from movement inside the storage area. Insects, rodents can be another cause of infesting perishable goods, thus proper sanitation is important. So skilled and specialists are essential for every job in the warehouse to reduce shrinkage due to handling goods improperly.
How to Prevent Inventory Shrinkage?
Cross Check System
The first thing any organization does is to implement multiple layers of quality checks and verification. Assign more than one employee to important assignments such as signing invoices, recording stock, and accepting stock. The second person ensures that any crucial details are not missed out on or any inaccuracy is there. It also helps eliminate fraud.
Employee Verification
While hiring a new employee do a proper background verification to understand the past. It helps you understand if the employee had any past record of stealing etc. You can understand the general conduct and behavior of the employee. If a potential employee has a long history of improper conduct, the company should drop them. The hired employees should be properly trained to handle inventory appropriately and carry out stock-taking.
Upgrade to Cloud-Based Inventory Management
When you upgrade your inventory management from paperwork to cloud-based system, you get every data within a smart dashboard that has access to all your inventory movements. Purchase orders, inventory report will give access to all the stakeholders in the organization with a centralized database. You can manage the supplier side, review, and monitor the stock list from the headquarters to eliminate any discrepancies. It also eliminates human errors with barcoding. It will track the location of the inventory from the point of origin to the point of sale and produce logs for all the users that logged into the system.
Regular Audit
A regular audit is essential to track the inventory shrinkage percentage over regular time intervals to measure any increase or a decrease in shrinkage. The inventory report should be compared to the previous inventory reports to understand any shrinkage. The regular checks provide a pattern of inventory shrinkage. A steady decline in shrinkage percentage confirms the techniques used are working out and a steady increase or zero increase implies the current measures are not able to bring the shrinkage down and you need to revisit your strategy.
Better Surveillance & Security
Track and keep all the areas of goods movement and warehouse under surveillance all the time. Installing cameras, RFID, Tagging will help reduce the shrinkage. The warehouses and storage areas should have restricted access. Whoever has access to the warehouse should go through a swipe card technology to trail movements in case anything is found missing in the future.
Empower, Give Rewards, and Make Employees Accountable
Make sure that each day the employees are leaving the premises ensuring they have done their part in keeping the shrinkage to the minimum. Empower them to take the decision to do the best for the interest of the organization. Rewards and appreciations work wonders to make employees take responsibility. When you make them accountable, they make sure nobody tampers with their part of the inventory.
Make Stricter Company Policy
Educate employees about the latest fraud trends and help prevent them from being fooled. Make them understand that when the company takes a hit due to shrinkage, they are going to get affected as well with the damage and losses as it will hamper their growth. In this way, they will put maximum effort to avoid any glitches or errors on their part.
Make Regular Maintenance Of Storage Area
Make regular maintenance of storage areas to avoid any rodents damaging your goods. Do regular pesticide treatments to keep the storage place free of pests. Even small negligence in sanitation increases the deteriorating rate of the goods stored and reduces their storage time. Keep the storage place well maintained to avoid any leakage of water or dust. A well-organized inventory always lasts long and minimizes wastage.
Conclusion
Although there are many unforeseen reasons that can hamper your inventory shrinkage, following the above methods and regular audits can help you reduce the shrinkage percentage drastically. This will eventually result in a higher profit for the organization.
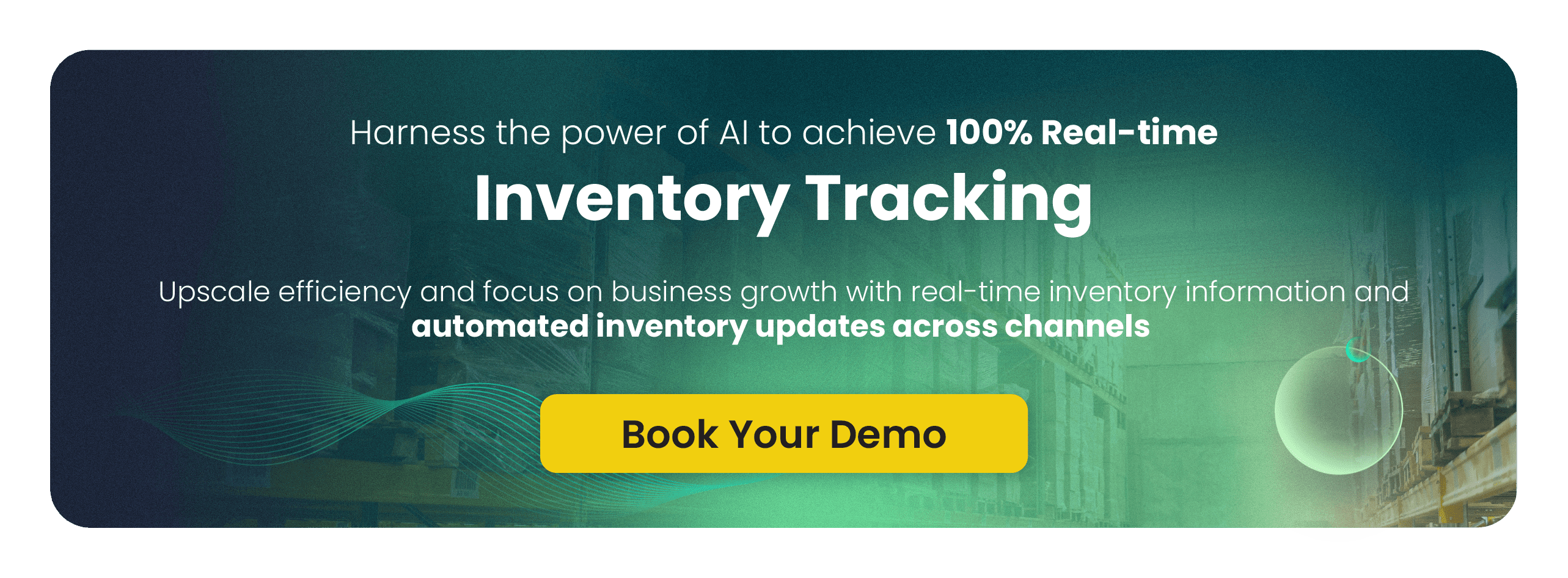