If you like being sure of your facts, inventory reconciliation is sure to pique your interest. It’s an efficiency practice businesses carry out to verify that the amount in their inventory lines up with the inventory recorded.
It’s never ideal to over-promise and underdeliver. But that’s what happens most of the time if you do not reconcile your inventory. The ensuing discrepancy can impact your business because it lessens how many customers get what they want.
In this blog, we’ll take a closer look at the improvements inventory reconciliation makes.
What is Inventory Reconciliation?
Inventory reconciliation matches stock records with what’s physically stored in warehouses. It compares the inventory count with the inventory record, thereby helping to catch discrepancies. If the numbers don’t add up, you can take the due investigative measures.
Inventory reconciliation isn’t about adjusting the numbers to create an exact match. Rather, it’s about identifying the reasons behind a mismatch turning up in the first place, and remedying it electronically or via manual inventory sheets.
Inventory reconciliation safeguards your business against inventory shrinkages and lost revenue through inaccuracies.
The 5 steps to reconcile inventory are
1. Perform a physical count
The first place to start would be your shelves. Spend a day recording the number of items in your inventory. If your inventory is split across different locations, you and the team can confirm if items are miscounted or wrongly entered.
2. Compare the physical count with record of inventory
Compare the counted inventory against your records. Team members should be able to confirm their physical presence against what you’re reading off the records. If the count seems higher or lower on either end, you can find out if it’s due to any of the following;
- Wrongly filed paperwork.
- Mathematical miscalculations
- Wrong categories.
- Falsified information from suppliers.
3. Go back to your last reconciliation
If this is the first time you’re reconciling inventory, use it for next time! But if you’ve reconciled stocks previously, go back for an explanation of the differences. Examine your shipment deliveries and sales invoices. In 90% of the cases, it comes down to a misreported SKU or mathematical error. If these are right, then it’s time to consider other possibilities such as someone skimming from the top or fraud.
4. Locate the discrepancy source
Once you find out where the discrepancy lies, you should create a reconciliation statement listing out the inaccuracies and make a note to update previous stock records on an inventory management system. The next course of action is to implement a Standard Operating Procedure to prevent future such incidents.
5. Reconcile repeatedly
While it isn’t possible to cover an entire warehouse in a single day, you need to create a fixed cycle for stock reconciliation to discourage discrepancies arising from human error, thefts, and fraud.
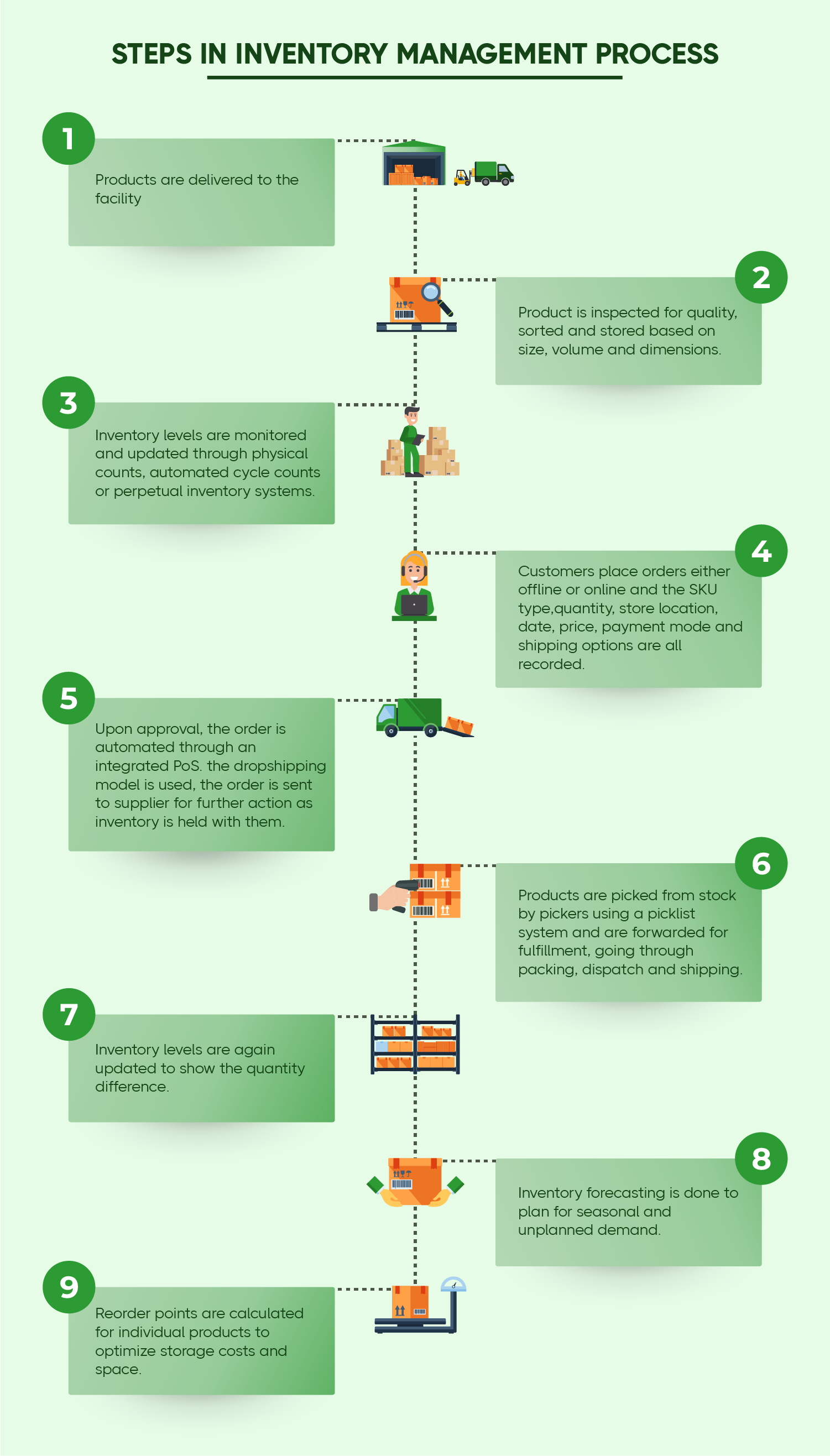
Steps to prevent inventory discrepancies
1. Regularize supplier Communication
Cultivate a culture of communication with your supplier's network to gain better inventory control. Your supplier should be able to provide inventory pipeline updates so that you can plan on receiving inventory and arranging for its storage by location. A dedicated channel for sharing updates not only creates mutual trust and understanding but can also cross-check that the quantities your supplier dispatched are received at the warehouses.
2. Use inventory reconciliation reports
An AI-driven inventory and warehouse management platform features warehouse and inventory reports and orders, sales, and returns reports. Under inventory reports, you can look at the reconciliation report, inventory planning by days, and shelf-wise stock reports to reconcile inventory records against what is manually entered by warehouse staff. It improves inventory tracking and helps you to identify and solve discrepancies as and when they occur.
3. Perform cycle counting
Cycle counting is a method to prevent inventory shrinkages and revenue losses. It counts the inventory by grouping them into categories so that you’re reconciling a small portion of the entire inventory until you cover it fully. The two most often used cycle counting methods are
3.1 The ABC method
The ABC method (AKA the Pareto law), categorizes products into three groups by their cost and/or turnover. Group “A” will comprise 20% of your top-performing products while Groups “B” and “C” will have the remaining 60 and 20 percent of the profit value respectively. It counts your best-selling products more frequently than the bottom performers
3.2 The Seasonal Method
The seasonal method is best suited to businesses that experience seasonal fluctuations, i.e holiday-driven and time-of-year sales. During such events, items that sell quickly are grouped and counted so that shelves can be restocked before going into the red. Items that are selling at the moment make it easier to monitor transactions and catch discrepancies
4. Reduce human errors with staff training
Carry out quality compliance checks at random for warehouses to understand the current practices and whether those could benefit from improvements. Educate your staff on stock keeping and counting, warehouse receiving, and inventory storage so that they are able to streamline manual and digitized entries.
5. Partner with a 3PL
Use a third-party fulfillment service provider with a wide network to handle shipments and deliveries.
Cycle counting best practices to follow
Cycle counting counts the stock on a category or time-specific cycle, contingent on the number of SKUs your business deals with. Inventory cycle counts examine disparities between the in-stock/ actual stock and the stock for sale.
- Refresh recorded inventory before carrying out a cycle count.
- Perform a monthly cycle count by category.
- Carry out a cycle count on the top-selling or best-performing stocks first.
- Use daily cycle counts if the SKU quantities allow for it.
- Create in-store merchandise accountability by allocating store sections to employees.
- Try daily cycle counts if your SKU quantity allows it
- Weigh goods if they cannot be physically counted or handled
- Separate the cycle counting and inventory recording roles.
Frequently Asked Questions
1. Why is physical inventory and reconciliation important?
Inventory reconciliation cracks down on fraudulent activities and theft and helps to reduce human errors. Using inventory reconciliation reports, businesses can
- Get inventory figures in writing against a physical inspection of the inventory.
- Record all types of inventory separately.
- Improve inventory tracking and
- Create an operational system of record to maintain procedural compliance.
2. How do you reconcile inventory in SAP?
- Go into the inventory module on Sap Business One. Under inventory transaction, select the first tab to open balances.
- Select the item codes, warehouse, properties, and groups.
- Apply the appropriate sort bys to the columns.
- Select the stock to hide or unhide.
- Under inventory posting, you’ll see that the inventory count is updated with differences.
- You can then hit the reconcile button on the bottom left panel of the posting module.
Reconciling inventory is especially important to retail businesses whose stock is constantly fluctuating from shipments and transactions. Corroborating inventory reports and physical cycle counts ensures accuracy and prevents stock mismanagement.
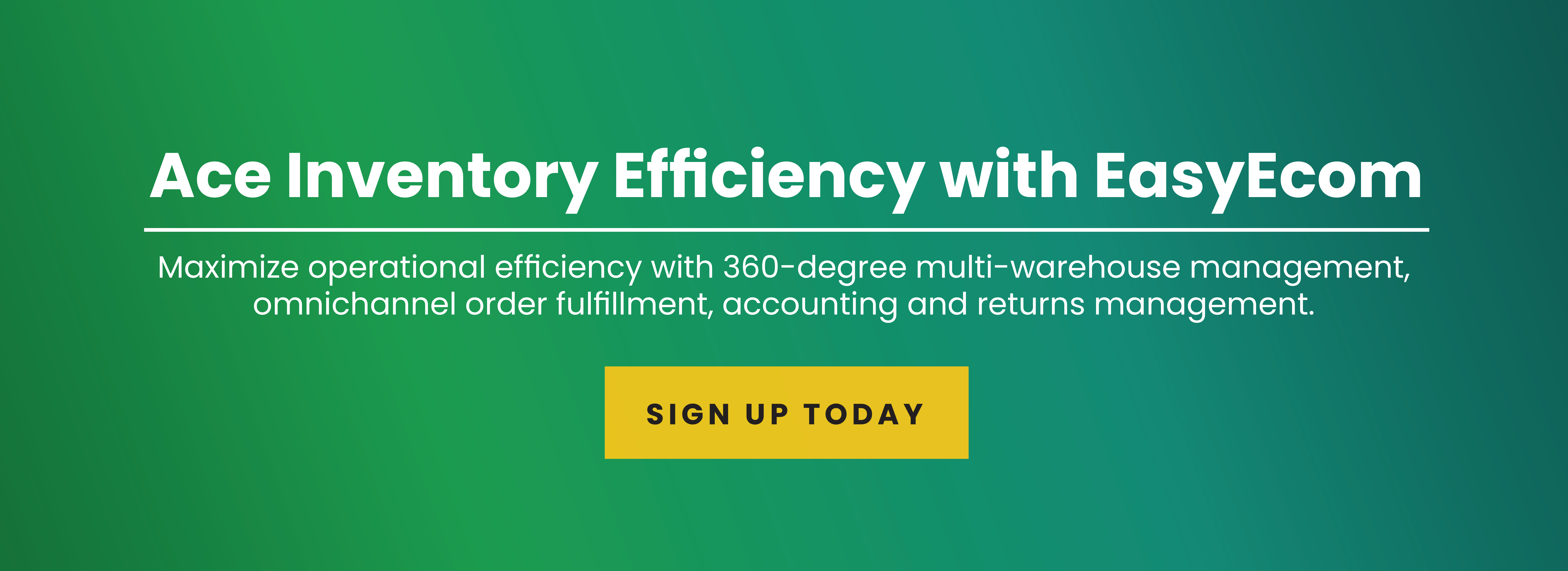